Things You Must Know about Casting Steel Parts
Know about Casting Steel Parts
Casting steel parts refer to components made from cast steel, exhibiting properties similar to cast iron but with superior strength. Currently, casting steel parts find extensive use in various fields such as shipping, automotive, construction machinery, and power station equipment. So, why are casting steel parts so popular, and what aspects showcase their process advantages and design flexibility? The following text provides a brief introduction.
One of the advantages of casting steel parts is their flexibility. Designers have maximum freedom in shaping and sizing castings, allowing for the production of both simple and complex components using relevant processes. The ease of shape alteration and rapid forming make casting steel parts advantageous, particularly for clients with urgent needs or short delivery cycles.
Due to the ability to select different chemical compositions and control the structure, casting steel parts are suitable for various engineering requirements, offering a wide application range. Additionally, casting steel parts can achieve different mechanical and application properties through various heat treatment processes, while also exhibiting excellent machinability.
The overall structural strength of casting steel parts ensures reliability in engineering. Coupled with the short delivery cycles, casting steel parts demonstrate clear economic advantages. Besides the mentioned benefits, another advantage during usage is the broad range of adjustable weight, making them applicable in various scenarios.
Casting steel parts are mainly categorized into cast carbon steel, cast low-alloy steel, and cast special steel products. Cast carbon steel includes low carbon steel (carbon content less than 0.2%), medium carbon steel (carbon content between 0.2-0.5%), and high carbon steel (carbon content greater than 0.5%).
With increased carbon content, the strength and hardness of cast carbon steel increase, providing casting steel parts with higher strength, plasticity, and toughness. This makes them suitable for heavy machinery components bearing large loads, such as rolling mill frames, hydraulic press bases, and applications in railway vehicles for manufacturing parts subjected to strong impact forces, such as side frames, wheels, and hooks.
Brief Overview of Common Process Defects in Casting Steel Parts
While casting steel parts are widely adopted due to numerous advantages, they still have inherent disadvantages. Common process defects during casting include porosity, inclusions, shrinkage, looseness, and cracks. The following section briefly introduces these common defects.
Porosity in casting steel parts occurs when the metal melt contains excessive gas, and the mold is damp with poor permeability, leading to the formation of voids. Inclusions are divided into non-metallic inclusions, formed during smelting reactions or by the inclusion of refractory materials during casting, and metallic inclusions, involving non-melted foreign metals falling into the steel melt.
Shrinkage defects result from insufficient volume contraction during the cooling and solidification of the metal melt in the casting process. Looseness refers to cracks or voids in the middle of casting steel parts' wall thickness due to poor smelting, resulting in a porous structure during casting.
In addition to the mentioned defects, cracks are also common, especially where there are abrupt changes in the cross-sectional dimensions of the casting.
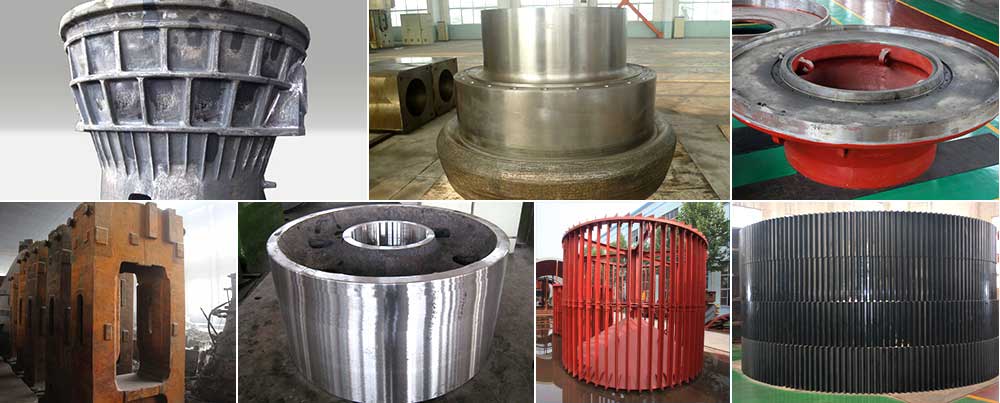
Four Considerations for Stainless Steel Casting
To prevent the formation of white spots during stainless steel casting, the wall thickness should not be too thin. The casting corners, especially for metal mold castings with a wall thickness of 15mm or more, should have rounded corners.
Due to the non-expandability of the metal mold and cores, the casting slope for stainless steel casting should be slightly larger than that for sand casting, typically 30%-50%.
Considering the rapid heat dissipation of the metal mold, the minimum wall thickness for stainless steel casting should be greater than that for sand casting.
The thickness of internal walls and ribs in stainless steel castings should generally be 0.6-0.7 times the connected external wall thickness to prevent cracking at the junction between internal and external walls during cooling and contraction.
Overview of Casting Steel Parts Inspection Methods
Casting steel parts are widely used in almost all industrial sectors today, especially in shipping, automotive, construction machinery, engineering machinery, power station equipment, and chemical equipment. Before casting steel parts are put into use, they need to undergo inspection to determine their quality and suitability for use. The following section provides a simple introduction to the inspection methods for casting steel parts.
For small to medium-sized casting steel parts, especially those with small volumes and light weights like investment precision castings, users can magnetize them in at least two roughly perpendicular directions on a fixed magnetic particle testing machine. It is advisable to use direct current and perform wet continuous inspection.
For larger and heavier casting steel parts, users need to magnetize at least two roughly perpendicular aspects of a specific area or zone using portable or mobile magnetic particle testing machines with direct current or half-wave rectification. Subsequently, the casting steel parts' local inspection can be carried out using the touch method.
During the inspection process, to prevent burning and electrode contact with the casting, users should avoid connecting the power supply when the electrode does not fully contact the casting surface. Only after the current has been disconnected can the electrode be removed. Additionally, clean and suitable electrodes should be used.