rolling mill stand
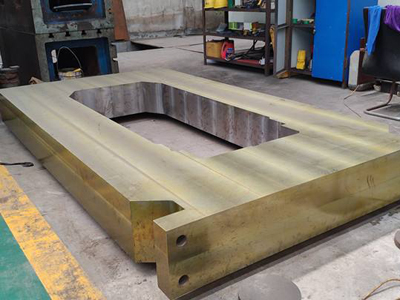
Rolling Mill Stand
Weight: 23-130 T
Applicable equipment: rolling mill
Application industry: metallurgical industry
Main material: ZG270-500
The rolling mill stand, also known as rolling mill housing, is an important part of the hot rolling, cold rolling, continuous rolling and other rolling mills, and is widely used in the metallurgical industry. The rolling mill stand is composed of two pieces to house the roller chock and the roller adjustment device so that it needs to have sufficient strength and rigidity to withstand the rolling force. There are two main types of rolling mill stand: closed type and open type. The closed-design rolling mill stand is an integral housing with high strength and rigidity which is mainly used in blooming mills and strip mills with large rolling force. The open-frame rolling mill stand is composed of two parts: the body and the upper cover, which is easy to replace the roller, and is mainly used for the belgian rolling mill.
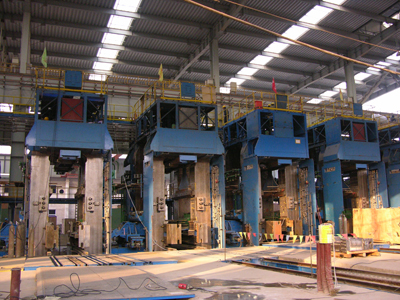

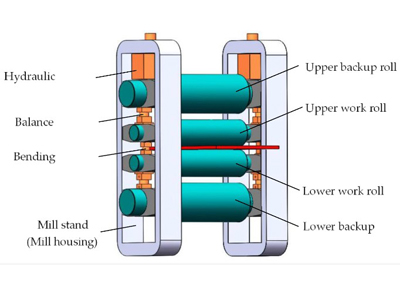
The rolling mill stand is an important part of rolling mill, and its weight accounts for 45~50% of the entire working stand. Due to the harsh working environment of the working process, the roller will cause great impact on the rolling mill stand through the bearing seat to bring the inner window surface and the bottom surface of the rolling mill stand with different degrees of corrosion and wear, which makes the gap between the stand and the roll chock is difficult to effectively control and manage and often exceeds the management limit. Therefore, the quality requirements of the rolling mill stand are strict, and the steel castings must not have casting defects such as inclusions, shrinkage holes, porosity, cracks, etc,. The rolling mill stand not only requires accurate dimensions, but also has high requirements on the mechanical properties of the steel castings.
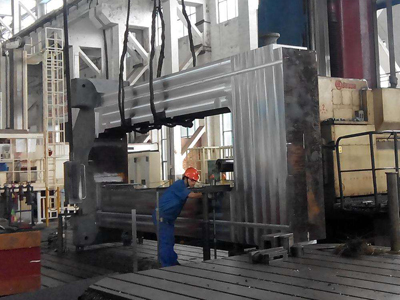
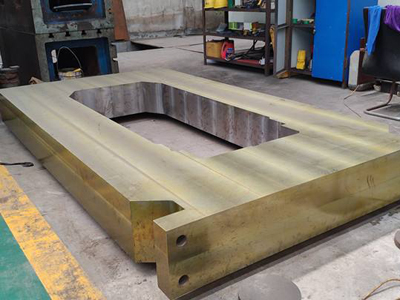
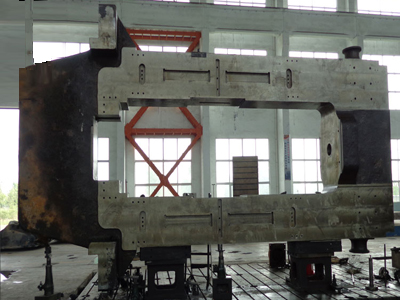
Why choose AGICO Cement's rolling mill stand?
1.The CAE casting simulation software
The software is adopted to ensure that the rolling mill stand has no shrinkage cavities, no shrinkage porosity, dense structure and good comprehensive mechanical properties;
2.Specific heat treatment method
Greatly enhances the wear resistance and impact resistance of the rolling mill stand, and prolongs the service life of the rolling mill stand;
3.High-quality steel
The unique polymer structure material endows the rolling mill stand with good impact resistance, greatly reducing the degree of wear and tear, and the material is not easily damaged even under the rolling force of up to 1900 tons. High-quality steel raw materials have good corrosion-resistant feature, which can protect the surface of the arch from the erosion of cooling water.
4.Metamorphic treatment and ladle bottom blowing argon technology
Strictly control the quality of molten steel, reduce the content of gas and harmful elements in molten steel, and improve the purity of molten steel, thereby ensuring the quality of rolling mill stand;
5.Flaw detection
The flaw detection of the inner window of the rolling mill stand reaches the secondary level to ensure the inherent quality of the rolling mill.
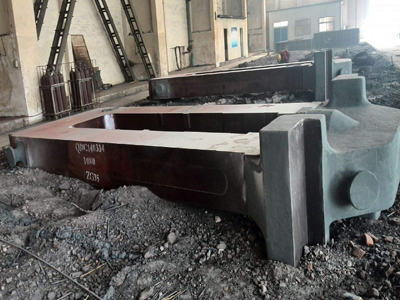
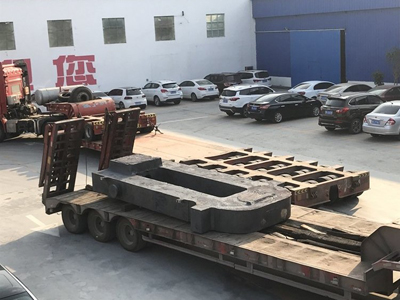
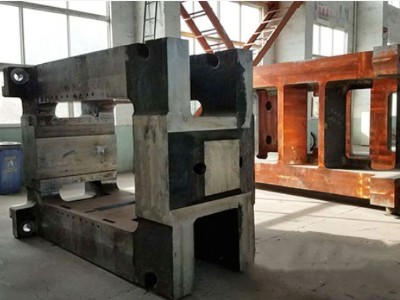
Casting process of rolling mill stand
1. Preparation of molding sand and core sand
The preparation process of molding sand directly affects the quality of molding sand. The preparation of molding sand is generally divided into the preparation and inspection of raw materials, and the preparation and quality control of molding sand.
2. Modeling
The method and process of making sand molds with molding sand and molds and other processing technology equipment can be called system modeling.
There are many types of modeling methods according to the shape, size and technical requirements of casting steel parts such as rolling mill stand.
3. Rolling mill stand smelting of large steel castings
The method and operation of heating and removing impurities in molten metal through metallurgical reaction, making the temperature and composition reach the specified requirements, and triggering smelting, and converting metal from solid to liquid state. There are many types of equipment used to smelt metals. We produce cast iron platforms, cupolas are often used for machine tool casting.
4. Sand dry
For some larger or higher quality large steel castings, dry casting is usually used. Such as large cast iron platforms, machine tool bed castings, machine tool workbenches, rolling mill stands, etc.
5. Pouring
The operation of pouring molten metal from a ladle into a mold is called pouring.
6. Clean up
The process of removing sticky sand, molding sand and excess metal from the rolling mill stand from the surface of the material can be called a cleaning.
7. Casting heat treatment
The process of heating a casting to a certain temperature range for a period of time, and then cooling it to an appropriate temperature at a specified rate to obtain the desired structure and properties is called casting heat treatment. The purpose of heat treatment of castings is to eliminate the casting stress of castings.