Common Problem of Air Lock Valve and Improvement by AGICO CEMENT
In the cement kiln pre-calciner system, the air lock valve plays a critical role in material separation and preventing airflow short-circuiting, thereby significantly contributing to energy saving and consumption reduction. Due to the harsh working environment, if the air lock valve is poorly designed or maintenance is inconvenient, it can lead to inflexible valve plate operation, resulting in poor sealing and internal air leakage. This can increase the overall system's thermal consumption, affect product quality, and reduce operational efficiency.
To address these technical issues, the new air lock valve design has undergone significant innovations and improvements, resolving common problems such as valve plate jamming and inadequate sealing. This article discusses the common technical issues encountered during the actual use of air lock valves and their solutions:
Air Lock Valve Shaft Jamming
Excessive Packing Compression
Most preheater air lock valves currently use packing seals. The principle is to apply a certain radial force to the packing to seal the gap between the air lock valve body and the moving valve plate shaft. However, this sealing method inevitably leads to a conflict between the flexibility and sealing of the rotating shaft. Greater radial force improves sealing but reduces the shaft's flexibility, while lower radial force increases flexibility but compromises sealing.
Solution: To address this issue, the new air lock valve design separates the contradictory problems of sealing and rotation. It features a three-layer sealing structure consisting of a labyrinth seal, packing, and oil seal from the inside out. The labyrinth and oil seals do not directly contact the rotating shaft. The labyrinth structure significantly reduces the instant positive pressure impact on the packing, allowing for a reduction in the radial pressure on the packing, thereby decreasing friction on the valve shaft. The outermost oil seal prevents external dust from entering the packing and further reduces leakage and prevents dust from escaping.
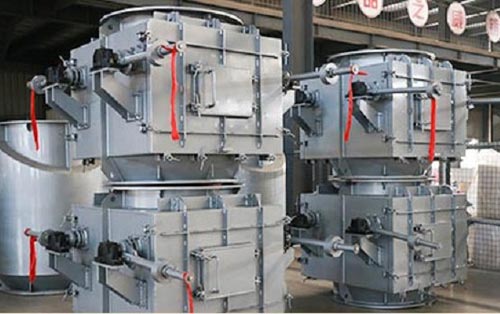

Air Lock Valve Shaft Deformation
Due to the large length-to-diameter ratio, air lock valve shafts are prone to deformation during use. Shaft deformation can damage the valve plate and potentially cause interference with other parts.
Solution: The new air lock valve uses heat-resistant steel casting for the valve shaft, with stress relieved through heat treatment. Professional tools are used to check and correct the shaft's straightness multiple times before assembly.
Interference Between Air Lock Valve Plate and Discharge Pipe
Traditional air lock valves often prioritize sealing when the valve plate is fully closed, typically adding a raised platform above the valve plate (see Figure 2). This reduces the contact area between the valve plate and the feed pipe, improving sealing. However, this design increases the likelihood of interference between the feed pipe and valve plate due to thermal expansion. To resolve this, the design must consider the coefficient of thermal expansion, optimizing the fit between the valve plate and feed pipe without compromising the valve's performance.
Solution: The new air lock valve uses 3D software simulation to optimize the contact surface between the valve plate and the feed pipe, designing chamfers at areas prone to interference. This ensures a gap of no less than 10mm between the valve plate and discharge pipe when the valve plate opens to 10° (see Figure 3), with the upper plane fully fitting against the discharge pipe when closed.
Air Lock Valve Plate Immersion in Castable
If the valve plate length is poorly designed, sudden impacts can cause the valve plate to open fully and become stuck in the castable, unable to reset for a long time. This situation not only allows air leakage but also risks damaging the castable.
Solution: The new air lock valve design uses 3D simulation to check the motion state and interference of all product models, adjusting valve plate length or optimizing casting parameters to fundamentally avoid interference with the castable.
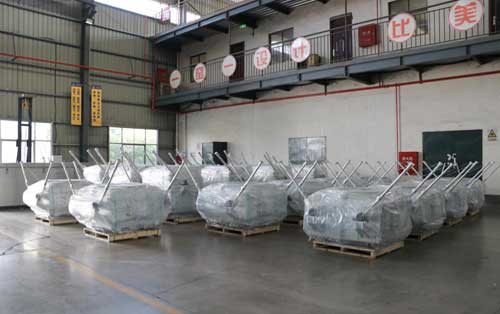
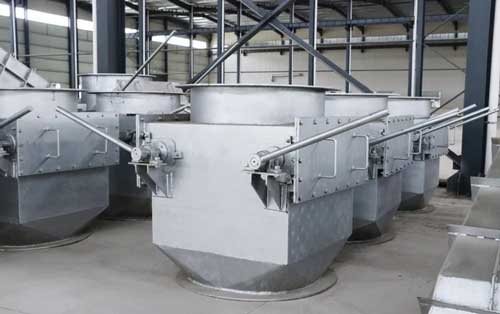
Internal Build-Up in the Air Lock Valve
Internal build-up in the air lock valve during use is unavoidable. When the build-up reaches a certain thickness, it inevitably affects the valve's flexibility. To address this, it is crucial to follow casting process guidelines strictly and select appropriate anti-build-up castables. In structural design, sufficient clearance should be left at key points for air lock valves in different discharge pipes to ensure that the build-up thickness does not interfere with the rotating parts during one operational cycle.
Solution: The new air lock valve design provides a 10cm clearance between the valve plate edges and the castable, with the castable cast using molds. Quality control measures ensure the flatness, volume density, and casting dimensions are within specifications. The valve body has a cleaning hatch for removing build-up, which has proven effective in practical use.
Other Factors
The smooth operation of an air lock valve is a systemic issue. Besides the four factors mentioned above, issues such as lack of maintenance for rotating supports (bearings, linear contact supports, sealing packing), deformation of components, low production and assembly precision, and improper installation position of the air lock valve in the discharge pipe can all affect its operation. Each stage of the air lock valve's design, installation, and use must be handled carefully, with regular inspection and maintenance.
AGICO CEMENT has made significant technical innovations and improvements over the past three years. The new air lock valve effectively addresses various technical issues encountered during the production design process. It not only reduces the heat consumption of the discharge pipe but also decreases the likelihood of kiln shutdowns due to problems with the discharge pipe. The new air lock valve has excellent air-locking capabilities, significant energy-saving effects, a flexible valve core operation, good sealing performance, and stable valve core operation. Customers have unanimously recognized the stability and cost-effectiveness of the new air lock valve, which has brought significant economic benefits to production enterprises and has strong potential for widespread application.