girth gear
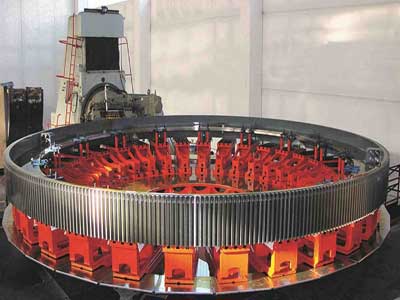
Application: ball mill, rotary kiln, chemical machinery, mining machinery, cement machinery, all kinds of large-scale machinery spare parts, etc
Size: 1t to 100 t (40 MT)
Material: steel, alloy steel, etc.
Quality Control: UT, MT, RT, PT, chemical composition test, mechanical property test, etc.
Heat Treatment: Normalize, Quenching, Tempering, Anealled.
Certificate:
1. Raw material certificate(material chemical compositon)
2. Heat treatment sheet report
3. Dimension inspection report
4. UT test report
Girth gear being the most common part in the cement industry is used to drive large rotating equipment like rotary kiln or horizontal mills while its function is to transmit and change the direction of force through the large ring gear.
Girth gear is generally composed of two to four segments that are assembled by counter screws together and tangentially fixed to the kiln body by spring plates.
As per Chinese standards, high-quality ZG45, ZG42CrMO and other cast steel materials are used along with unique heat treatment to improves the hardness, wear resistance and impact resistance. Ausferritic spheroidal graphite cast iron is also used for the production of girth gears(which is a cast alloy, iron, carbon and silicon).
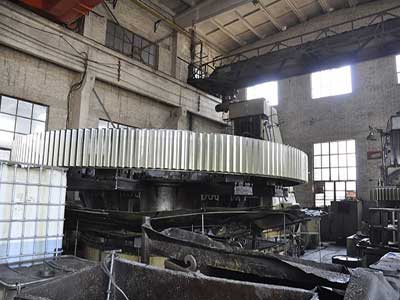
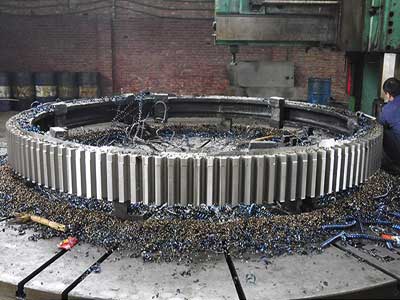
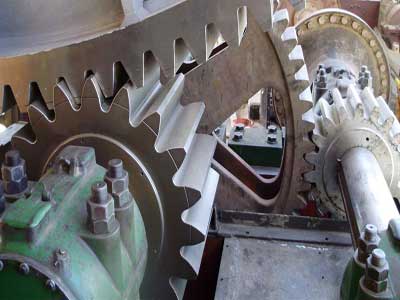
Why choose AGICO Cement's girth gear?
The clear majority of published knowledge about gear manufacturing relates to two main subjects: material quality and tooth accuracy.
Girth gears are very large non-rigid structures that require special care during the machining of individual mating segments as well as the assembled gear blank itself.
It is well known that a gear blank's mounting surfaces must possess certain measures of geometric accuracy, and that the gear's pitch cylinder must bear certain geometric relationships to those mounting surfaces. Moreover, the finest construction materials and the most precise tooth geometry have limited bearing on realized life when these geometric cardinal rules are not upheld. Indeed, the American girth gear rating standard — ANSI/AGMA 6014-B15 — disclaims validity when the required geometric relationships are not achieved.
However, the R&D department of AGICO Cement has committed to meet the highest standard of girth gear manufacturing and has achieved its goal and striving for excellence.
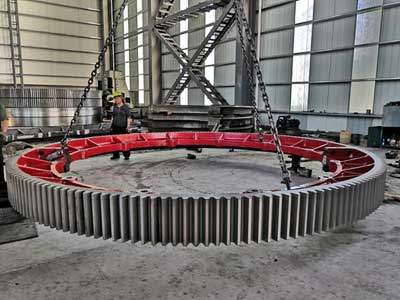
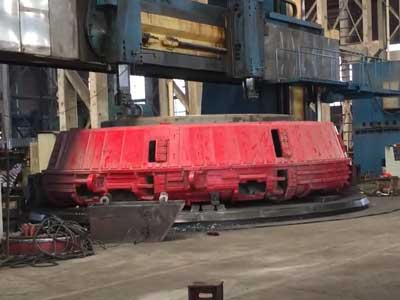
Our standard manufacturing technique
AGICO Cement's cutting-edge production methods ensure that our girth gears provide optimal power and stable operation for your mill or kiln, with high wear resistance and long run times. Our manufacturing process of girth gear has five steps, including final welding and rigorous quality checks after tooth cutting:
1. First, the raw material is rolled and forged to the required ring size.
2. The webs, splits and connecting plates are welded to the forged rim material according to a specific qualified process.
3. The components undergo strict non-destructive testing and then undergo post-weld heat treatment.
4. Coarse and fine chips trim girth gear to final size
5. Finally, as part of a closed examination, measuring and recording tooth's geometry, beat, hardness and many other properties.
.jpg)
Production Process Of girth gears
2.Explore feasibility with customer and R&D department
3.3D Design
4.Production
5.Rough parts manufacturing
6.CNC Machining
7.Fitting&Finish
8.Measurement&Check
10. Trial Production
11. Correction
12. Final Trial
13. Samples Inspection
14. Sample Approval by customer
15. Approval