feed chute
Rotary kiln inlet and outlet chute
During the working process of the rotary kiln, the raw meal powder is fed into the kiln barrel from the inlet chute at the high end of the kiln tail barrel. Due to the inclination and slow rotation of the kiln barrel, the material rolls along the circumferential direction and also rotates along the kiln. The composite motion moves axially from high temperature to low end. The raw meal passes through the process of decomposition and firing in the kiln, and after firing the cement clinker, it is discharged from the bottom end of the kiln cylinder and enters the cooler.
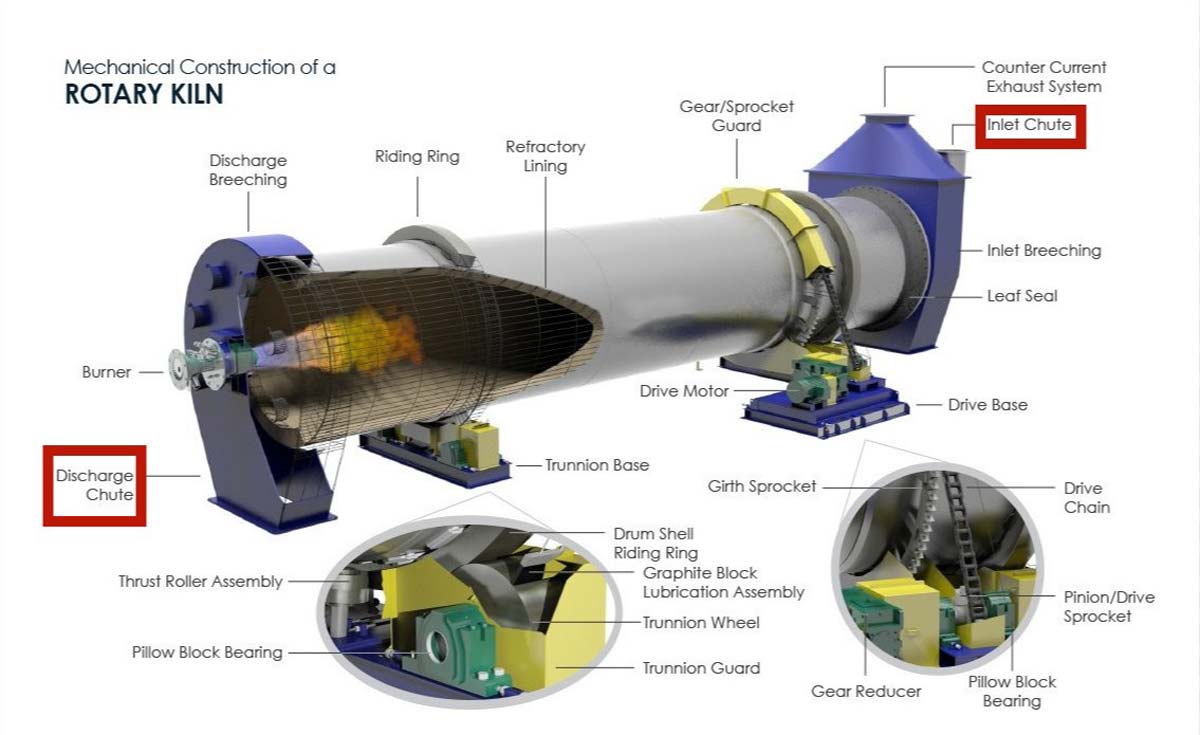
The outlet chute of the rotary kiln is installed on the transition section at the end of the rotary kiln, and is inserted obliquely into the kiln barrel through the transition section. The raw petroleum coke is transported from the pre-forging silo to the unloading chute through the quantitative feeder, and then enters the rotary kiln through the outlet chute for high temperature calcination. Therefore, the safety and reliability of the outlet chute is very important for the normal operation of the rotary kiln. Due to the high temperature in the rotary kiln, the general heat-resistant steel cannot withstand the high temperature of 1000℃ for a long time. AGICO's outlet chute is made of special steel, which is resistant to high temperature and high reliability.
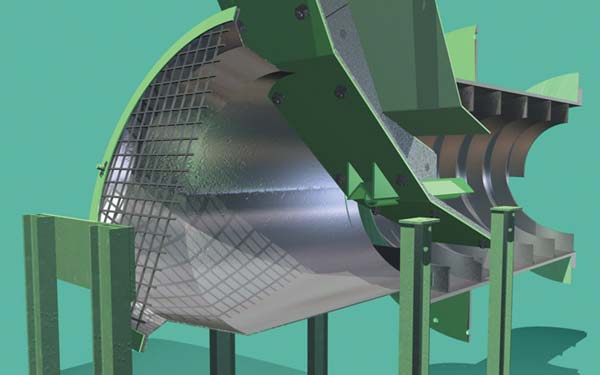
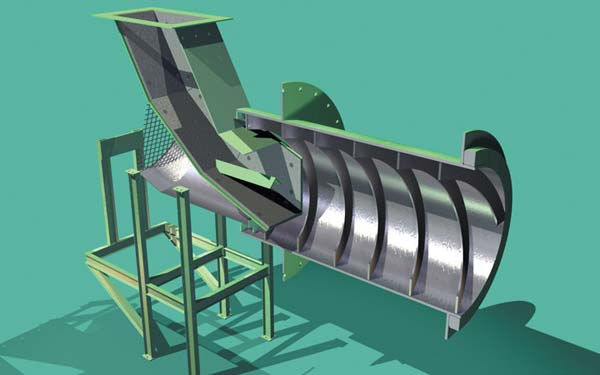
Ball mill feed chute
The material enters the conical sleeve in the hollow neck of the ball mill through the ball mill feed chute, and slides down into the ball mill along the cylinder wall. The section of the mill feed chute is oval. The inclination angle of the mill feed chute should be greater than the angle of repose of the material to ensure the smooth flow of the material. The structure of the chute feeding is relatively simple, but the amount of feeding is small, and it is more suitable for the use of the hollow journal with a large length and a short length.
The material enters the ball mill barrel through the ball mill feed chute. The output of the mill has a great relationship with the feed amount of the feed chute, so the design of the feed chute is particularly important. The inclination angle of the mill feed chute needs to take into account the natural repose angle of the material to ensure that the material can also slide down into the barrel of the ball mill by its own gravity, especially for some materials with a relatively large viscosity coefficient, it is easy to agglomerate in the feed chute, As a result, the material blocks the feeding chute, and the feeding is not smooth, which affects the output of the mill. AGICO Cement provides a mill feed chute that is easy to clean, aiming at the defects of the prior art. The use of feed chute with wear-resistant lining can effectively improve the wear resistance of the feed chute, reduce the wear and impact damage to the feed chute caused by ore and cast iron balls, improve the service life of the feed chute, and reduce replacement. frequency, ensure the production efficiency of the ball mill and reduce the production cost.
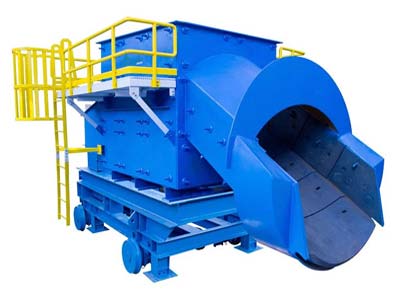
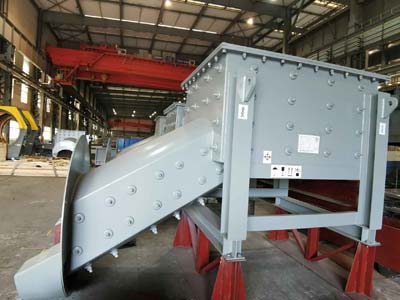
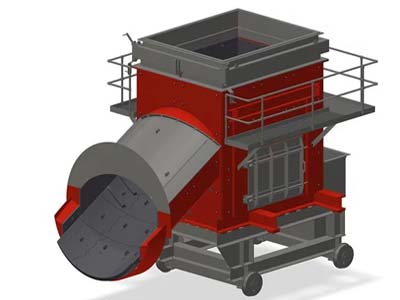