slag pot
Product: Slag pot
Weight: 1-150 Tons
Material: ZG230-450, ZG270-500, ZG310-570, ZG340-640 steel and so on
Application: Metallurgy, mining, chemical industries
Customizable: Yes
Certificate: CE, RoHS, GS, ISO9001
Type: Sand casting
Order quantity: 100 pieces per year
Sand Core Type: Clay sand core
Surface Treatment: Polishing, sandblasting
The slag pot is an important equipment for steel-making in the metallurgical industry. It is a container used to contain the high-temperature slag produced in the steel smelting process. It has a bowl-shaped container with hoisting trunnions on both sides.
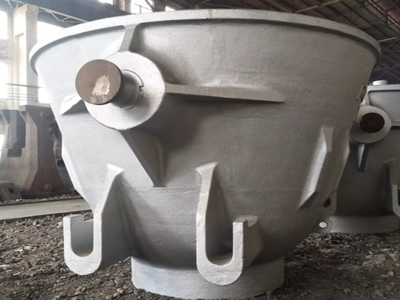
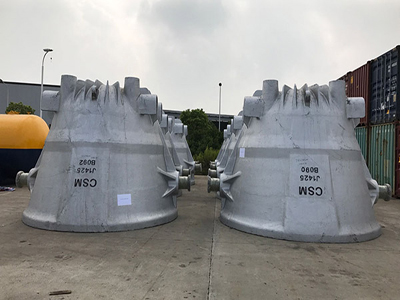
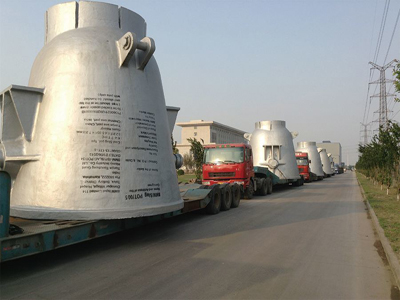
Customize your Slag Pot with our customization service
Introducing our unparalleled customization service, where years of experience and a dedicated team of skilled professionals come together to deliver excellence and reliability. At our core, we prioritize precision engineering and meticulous attention to detail, resulting in high-quality, customized slag pots that enhance your operational efficiency and productivity.
Key features that set our customization service apart:
- Unparalleled Expertise: Our team of experts possesses extensive knowledge and expertise in the intricate field of giant steel parts casting. Through successfully handling numerous complex projects, we have consistently exceeded client expectations. When entrusting us with your slag pot customization needs, rest assured that you are placing them in the hands of capable professionals.
- Seamless Collaboration: We firmly believe in building strong partnerships with our clients. By working closely with you, we gain a comprehensive understanding of your unique requirements. Throughout the process, we provide expert guidance and valuable suggestions, ensuring that the final product not only meets but exceeds your exact specifications and expectations.
- Tailor-Made Solutions: We recognize that no two steel casting operations are alike. Understanding the importance of customization, we offer a range of modifications tailored to your needs. Whether it be design, dimensions, capacity, or any other aspect of the slag pot, our capabilities enable us to deliver a bespoke solution precisely fitting your requirements.
- Superior Quality: Commitment to excellence permeates every stage of our manufacturing process. Employing advanced technologies, stringent quality control measures, and the use of the highest-grade materials, we ensure that our customized slag pots exhibit exceptional durability, longevity, and performance. With us, you can expect nothing less than superior quality.
- Timely Delivery: We understand the paramount importance of meeting deadlines in your operations. To that end, we have streamlined our production processes, implemented efficient project management techniques, and established robust logistics. These measures enable us to deliver your customized slag pots within the agreed-upon timeframe, without compromising on quality.
- Comprehensive Support: Our dedication to client satisfaction extends beyond the mere delivery of the product. We provide comprehensive after-sales support, including maintenance guidance, technical assistance, and responsive customer service. Should you have any queries or concerns, our team is readily available to address them promptly and effectively.
Choose our customization service for your slag pot needs and experience the perfect blend of expertise, collaboration, tailor-made solutions, superior quality, timely delivery, and comprehensive support. Together, we can elevate your operations to new heights.
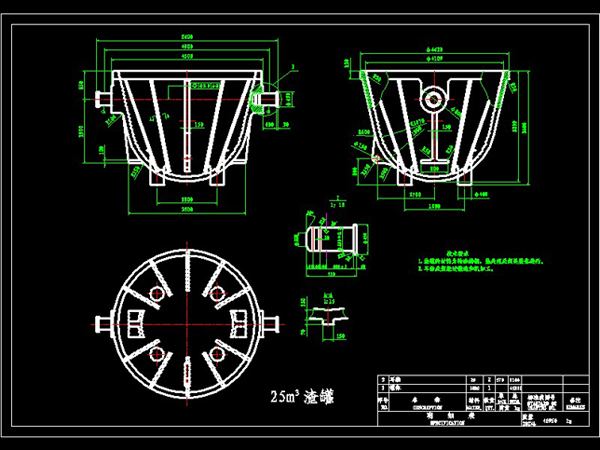
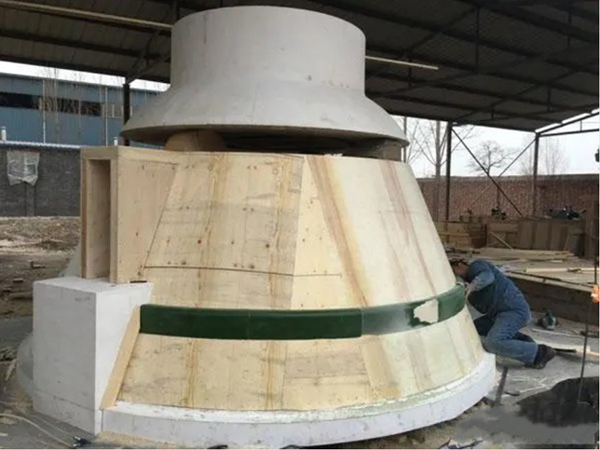
Advantages of AGICO Slag Pot
1.2000+ times of usage
Unlike slag pot from other brand which has the service life of 400-600 times of usage, AGICO Cement's slag pot can be used for more than 2000+ times. Service life increased by 20%.
2. Simulation&modeling before producing
Before pouring, the casting process is digitally simulated by CAE software to analyse the process and predict quality of the molding process of the product, which will further optimize the process of slag pot casting. The water glass sand molding process is applied with complete metallurgical auxiliaries to prevent the occurrence of hot cracks in castings and control its overall size. Meanwhile, pit modeling method applied in the process will not affected by the season and enjoy high production efficiency.
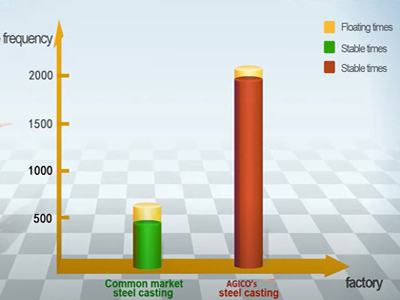
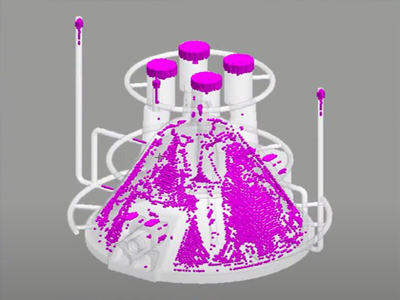
3. Pouring&heat treatment
The raw and auxiliary materials that pass the inspection are put into the electric arc furnace for smelting in proportion. The molten iron sample is sampled for spectral analysis. After it is qualified, it is poured in accordance with the principle of "low temperature and fast pouring", and the pouring time and temperature are recorded. In view of the problem that the carbon content difference between the two materials of trunnion alloy steel and tank carbon steel is relatively large, AGICO Cement has customized a complete set of processes to strictly control the welding problems in the production process.
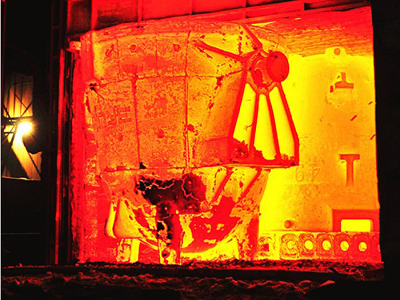
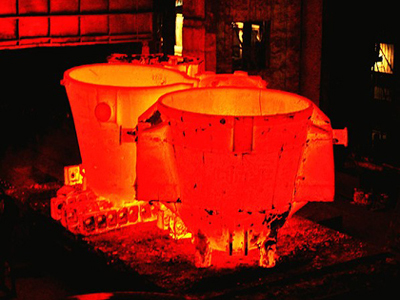
4.Grinding&shot blasting
Operations such as cutting, pouring, and flashing are carried out after the above processes. AGICO Cement has a professional grinding and finishing team and large-scale shot blasting equipment, which can effectively improve the appearance quality of the slag pot and make its surface quality meets customer’s requirements. The internal quality of the slag pot is strictly prohibited from leaving any defective products.
5.Slag pot from reliable manufacturer
AGICO Cement has strong capabilities of casting, processing and assembly which can provide customers with 150 tons / piece of large carbon steel castings, manganese steel castings, high-alloy steel castings and other cast steel parts. AGICO Cement's high-quality slag pot are exported to the United States, Germany, France, Italy, India, Indonesia, South Korea, Turkey and other more than 60 countries and regions.
.jpg)
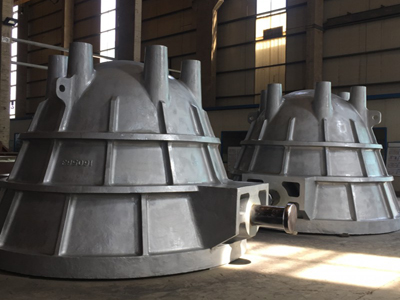
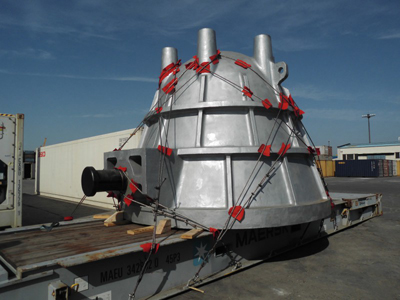
Common problem of slag pot
In production practice, the use of slag pots in ferroalloy smelting mainly has the following problems:
1. Due to the design of the overflow port of the slag pot, the center of gravity of the slag pot is offset. The slag pot is inclined during the lifting process and the slag liquid is easy to overflow which has a great hidden danger.
2. The overall structure of the slag tank is unreasonable. After being subjected to thermal stress, cracks are easily generated, and cracks will cause piercing.
3. It is designed to use one lined ladle and three slag pots. Sometimes too much molten iron will overflow from the ladle to the slag tank, causing the temperature at the bottom of the slag tank to rise sharply, which will cause damage to the slag pot.
Improvement measures of slag pot producing by AGICO CEMENT
1. Thicken the wall thickness inside the slag pot so that the center of gravity can be balanced after the slag pot is lifted.
2. The improvement part is to cancel the upper reinforcing edge of the slag pot, the bottom, middle and upper part of the slag pot are thin and uniform. The bottom reinforcement edge is reserved for expansion joints, and the bottom is added with strong ribs.
3. Change the structure of the tapping car from the original combination of one lined hot metal ladle and three slag pots to two lined hot metal ladles and two slag pots, which can effectively prevent the molten iron from flowing into the slag pot (which will cause local high temperature damage to the slag pot).

Based on the structural characteristics and quality requirements of the slag pot, the selection of a suitable casting scheme and process parameters is of paramount importance. Necessary measures should be taken to address issues such as axis looseness, shrinkage cavities, cracks, and the occurrence of air bubbles, particularly at the T-shaped reinforcement, in order to ensure the quality of the castings.
Considering the structure and solidification characteristics of the slag pot, the method of casting with the pot opening facing downward and using a concentrated riser system is adopted as an effective means to achieve sequential solidification of the entire casting and meet dimensional accuracy requirements. The advantages of this approach include employing a combination of multiple stacked, staggered, and vertical pouring molding boxes, sand beds prepared within the pit, and in-situ pouring. These facilitate convenient sand collision during casting, reduce buoyancy in the middle, eliminate the need for flipping or moving throughout the entire molding process. Additionally, the use of sufficiently rigid sandboxes and appropriately weighted iron plates helps prevent deformation and the occurrence of mold lifting. Moreover, after pouring, the risers can be hot-cut in situ within the original pit while cooling is carried out outside the pit, enabling the interleaving of several processes, shortening the production cycle, and effectively increasing productivity and the utilization rate of the molding area.
.jpg)
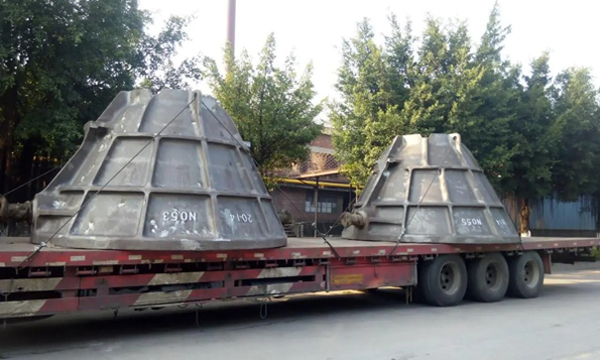
Factors need to be considered when using slag pot
Improper design of the overflow opening of the slag pot can cause the center of gravity to shift, resulting in tilting and overflow of slag, posing safety hazards.
If the overall structural design is not reasonable, the issue is not related to the center of gravity but rather the potential for crack formation and even puncturing of the slag pot, leading to accidents.
To address these design issues, it is necessary to consider potential problems during the design phase and make appropriate modifications during the casting process. Large-scale steel casting manufacturers should reinforce the rear section of the slag pot or increase the wall thickness based on the design drawings to achieve a balanced center of gravity. The overall structural design should eliminate reinforcement on the upper edge of the slag pot, while ensuring uniform thickness in the bottom and upper-middle sections. Additionally, it is important to pre-allocate expansion gaps at the bottom and reinforcement edges.
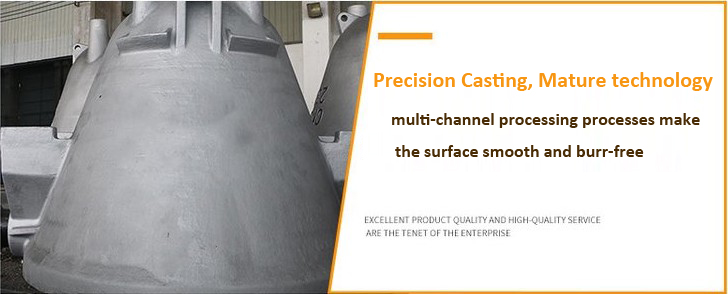
Factors that affect the lifespan of slag pot
There are various factors that can affect the lifespan of a slag pot, including abnormal slag from the converter. This includes furnace cleaning slag and high-temperature, high-oxidation iron slag produced during the smelting of special steel. The generated steel slag has higher temperature, higher iron oxide content, and better fluidity compared to conventional slag. When entering the slag pot, the iron oxide in the slag reacts with the slag pot itself, combined with the thermal shock from the slag, which can lead to incidents of puncturing. To mitigate this, large-scale steel casting manufacturers implement slag pot coating technology. The application of a high-temperature resistant and erosion-resistant coating layer on the interior of the slag pot reduces wear, improves slag removal rate, facilitates slag pot turnover, and effectively eliminates smoke pollution caused by steel slag turning over.
Construction process of wood mould of slag pot
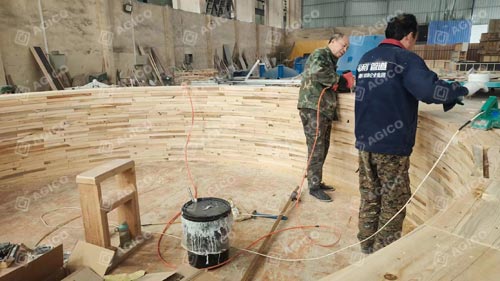
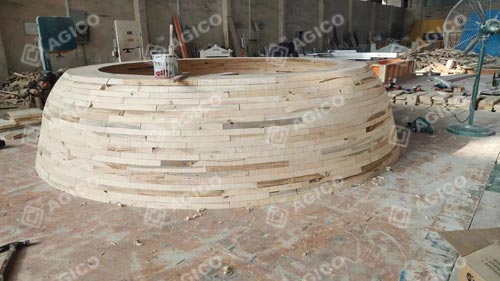
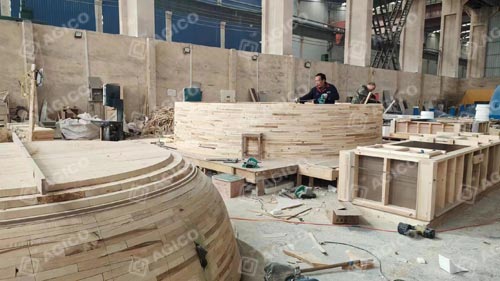
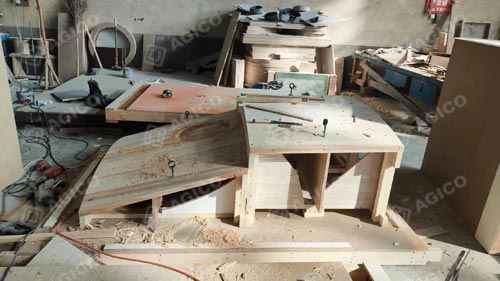
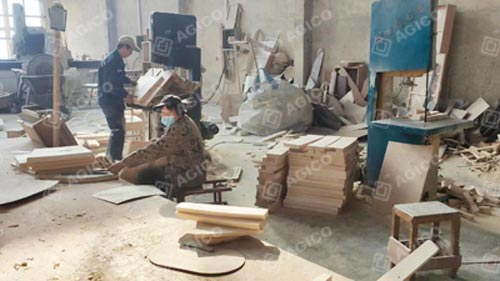
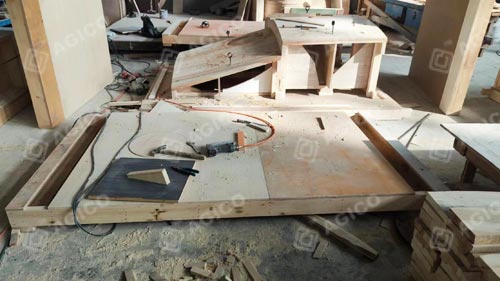
FAQs about slag pot
What is a Slag Pot?
A slag pot is a crucial piece of equipment used in metallurgical and mining operations. It is a large container or vessel designed to collect and transport molten slag, a byproduct of the metal smelting or refining process. Slag, which is the waste material formed during the separation of metal from its ore, is typically in a liquid or semi-liquid state at high temperatures. The slag pot is built to withstand these extreme temperatures and safely contain the molten slag until it can be removed and further processed or disposed of.
What are the Components of a Slag Pot?
A slag pot consists of several key components that work together to ensure its efficient and safe operation. The main parts of a slag pot include:
1. Shell: The shell is the outermost part of the slag pot and is made of high-quality steel or other suitable materials. It provides structural integrity and prevents leakage of the molten slag.
2. Trunnions: Trunnions are the supports or bearings on which the slag pot rotates. They allow the pot to tilt and pour the molten slag when required.
3. Lining: The lining of the slag pot is made of refractory materials that can withstand the high temperatures of the molten slag. The lining protects the shell from excessive heat and corrosion, extending the pot's lifespan.
How is a Slag Pot Used?
The usage of a slag pot involves several steps to ensure the safe and efficient handling of molten slag:
1. Preheating: Before using the slag pot, it is preheated to avoid thermal shock when it comes into contact with the hot slag. Preheating also helps in reducing heat loss during slag transfer.
2. Positioning: The slag pot is positioned under the slag discharge point, usually by an overhead crane or other lifting equipment. Proper alignment is crucial to ensure a smooth and accurate pouring process.
3. Pouring: Once in position, the molten slag is poured into the slag pot. The pot can be tilted to facilitate the pouring process. Care must be taken to prevent splashing or overflow of the slag.
4. Cooling and Solidification: After the slag is poured into the pot, it gradually cools and solidifies. The cooling process can be accelerated by water or air cooling methods, depending on the requirements.
5. Removal and Further Processing: Once the slag has solidified, the slag pot is removed from the area. The solidified slag can be further processed for various applications or disposed of properly.
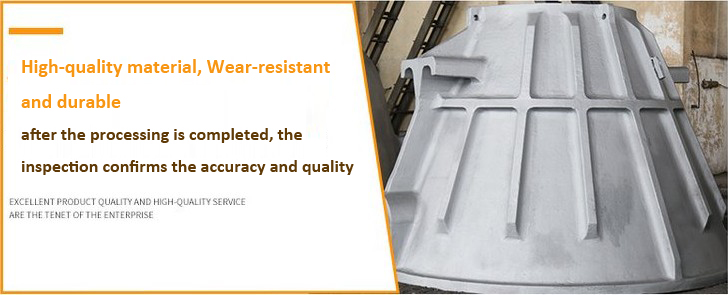
What are the Advantages of Using a Slag Pot?
The utilization of a slag pot offers several advantages in metallurgical and mining operations. Some key benefits include:
1. Efficient Slag Handling: Slag pots enable efficient collection and transportation of molten slag, reducing the risk of spillage or accidents. The large capacity of slag pots allows for the accumulation of significant amounts of slag, minimizing the frequency of emptying or replacing the pots.
2. Improved Safety: Slag pots are designed with safety features to handle the extreme temperatures and corrosive nature of molten slag. They help prevent the escape of slag, minimizing the risk of burns or injuries to workers. Additionally, proper handling and pouring techniques reduce the chances of splashing or overflow.
3. Cost Savings: By efficiently collecting and transporting molten slag, slag pots contribute to cost savings. They help prevent the loss of valuable metal content in the slag, which can be further processed or recovered. Additionally, the durability of slag pots reduces the need for frequent replacement, resulting in long-term cost efficiency.
What Factors Should be Considered when Choosing a Slag Pot?
Several factors should be taken into account when selecting a slag pot for a specific application. These factors include:
1. Capacity: The capacity of the slag pot should match the volume of slag generated during the metal smelting or refining process. It is important to choose a pot with adequate capacity to avoid frequent interruptions for emptying or replacing the pot.
2. Material and Lining: The choice of material for the shell and the lining depends on the type of slag and the operating temperature. The material should be resistant to heat, corrosion, and wear. The lining should be made of refractory materials capable of withstanding high temperatures.
3. Design and Construction: The design and construction of the slag pot should ensure structural integrity, stability, and ease of handling. Considerations such as trunnion arrangement, reinforcement, and accessibility for maintenance should be taken into account.
4. Safety Features: The slag pot should have appropriate safety features, such as splash guards, thermal insulation, and ergonomic design, to protect workers from potential hazards.
5. Cost and Longevity: While considering the initial cost, it is important to assess the longevity and durability of the slag pot. Choosing a high-quality pot that can withstand the operational demands and has a longer lifespan can result in cost savings over time.
What are the Maintenance Requirements for a Slag Pot?
Proper maintenance of a slag pot is essential to ensure its longevity and optimal performance. Some key maintenance requirements include:
1. Regular Cleaning: Slag pots should be cleaned thoroughly after each use to remove any solidified slag or debris. This helps prevent buildup and potential damage to the lining or shell.
2. Inspection and Repair: Periodic inspections should be conducted to identify any signs of wear, cracks, or damage. Any issues should be addressed promptly to prevent further deterioration and ensure the pot's integrity.
3. Lining Maintenance: The refractory lining of the slag pot is subject to wear and erosion due to the corrosive nature of molten slag. Regular checks and maintenance of the lining, such as patching or relining, are necessary to maintain its effectiveness.
4. Cooling System Maintenance: If the slag pot has a cooling system, regular maintenance of the cooling pipes or channels is required. This ensures efficient cooling and prevents overheating or damage to the pot.
5. Storage and Handling: When not in use, slag pots should be stored in a dry and protected area to prevent corrosion and damage. Proper lifting and handling techniques should be followed to avoid stress or structural deformation.