roller shaft
Roller shaft for roller press
Introduction
Roller press, also known as extrusion mill and roller press mill, is a new type of cement energy-saving grinding equipment developed in the mid-1980s in the world. It can replace the ball mill pre-grinding system with high energy consumption and low efficiency, and can reduce steel consumption and noise. Function, suitable for the construction of new plants, and can also be used for technical transformation of old plants, so that the output of the ball mill system can be increased by 30-50%. After extrusion, the 0.08mm fine material accounts for 20-35%, and the smaller than 2mm accounts for 65% to 85%. The internal structure of small particles is filled with many tiny cracks due to extrusion, and the wearability is greatly improved. The main body of the roller press, especially the roller shaft of the roller press, is the basis for manufacturing the roller press. Only good processing equipment, processing technology, and perfect testing methods can be used to process and manufacture products with superior performance and reliable quality .
AGICO Cement adopts a new roller shaft and roller shaft method to replace the overall roller mill, and builds a wear-resistant layer by surfacing. The new roller shaft structure can select materials and heat treatment processes according to the different requirements of the grinding roller shaft and sleeve, which not only ensures the strength requirements of the shaft, but also improves the welding performance; the new roller shaft structure can increase the number of on-site repairs, reduce operating costs, and shorten maintenance time. When the wear is beyond repair, only the roller shaft needs to be replaced, and the shaft can be reused; the maintenance cost is greatly reduced.
Application
Main application: Mining, cement, coal chemical industry, steel slag, thermal power and other crushing treatment.
Product features: Relying on the company's advantages in the field of wear-resistant materials, the roller shaft is specially developed, which greatly improves the wear resistance and impact resistance of the rolling roller and prolongs the service life. AGICO uses the unique centrifugal composite technology , to achieve "outer hardness and inner toughness", and centrifugally cast the surface bite pattern. Compared with the surfacing roller shaft, it eliminates the defects such as peeling and falling blocks caused by surfacing welding, so as to realize life-long surfacing maintenance-free, use The service life is more than 3 times that of surfacing roller shaft.
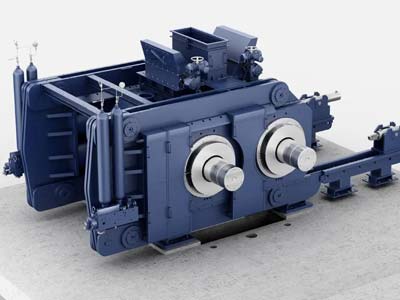
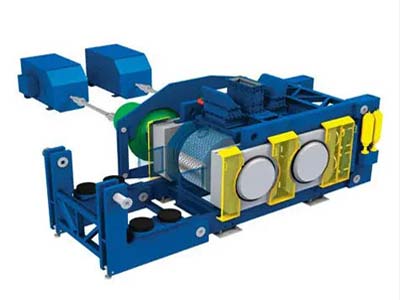
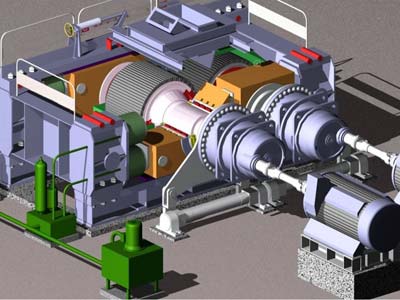
At present, the roller shaft produced mainly adopts forgings, and a wear-resistant layer is surfacing on the surface to improve its wear resistance. However, because the roller shaft is subjected to repeated cutting and wear of materials during rolling and crushing, and the periodic alternating pressure and repeated wear caused by the huge pressure in the work, the surface of the roller shaft produces grooves and convex ribs, and the surfacing layer on the surface is very easy. There are cracks and wear phenomena, which will damage the parts faster and shorten the service life. It needs multiple surfacing welding repairs, and is limited by many factors such as the production site. It is difficult for the surfacing welding to meet the standard requirements, which seriously affects the use of the roller press. efficiency. AGICO Cement achieves optimization by:
The material ratio of the outer layer of the roller shaft is optimized, and the content of alloy elements in the outer layer is increased to ensure that the wear resistance and fracture toughness of the roller shaft are improved. Alloying elements form various carbides in the product structure, and also affect the transformation characteristics of the metal matrix. The hardness, morphology, quantity, distribution of carbides and the structure and properties of the metal matrix play a decisive role in the wear resistance, toughness and other properties of the product. By increasing the content of C, Cr, Mo, V, W and other alloys, the matrix can be strengthened and the total amount of carbides can be increased, which is beneficial to the smoothness of the friction surface of the roller shaft.
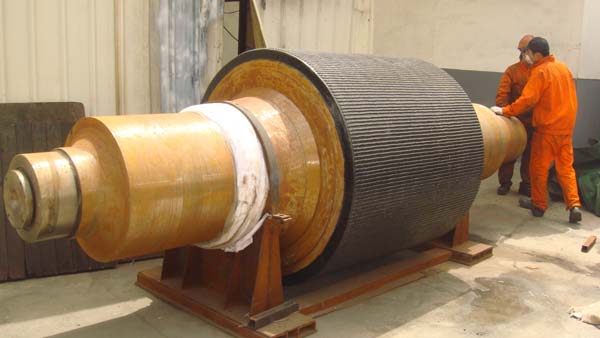
Reasonable centrifugal compound casting process is adopted to achieve metallurgical combination of inner and outer layers, and the combination state is good. 3. According to the characteristics of the high alloy of the roller shaft, formulate a suitable heat treatment process, especially by increasing the tempering temperature, through multiple tempering processes, the fracture toughness of the roller shaft is strengthened; through the above inventions, the original problem of forging and welding the roller shaft is completely solved. Peeling, peeling, falling blocks, troublesome repairs, and expensive welding rods. After verification, the outer layer hardness of the roller shaft of the present invention is 60-64HRC, the impact toughness is 12J/c㎡, the inner layer hardness is 26~30HRC, the tensile strength is 800/900Mpa, the yield strength is 730Mpa, and the service life is longer than that of the previous forged surfacing roller shaft Improve more than 2 times.
AGICO Cement roller press rollers have a firm structure and long service life, which can effectively reduce maintenance costs and are safe to use. At the same time, the company has 20 years of precision forging experience, and its products are exported to South Korea, Japan, Russia, Brazil and other countries.
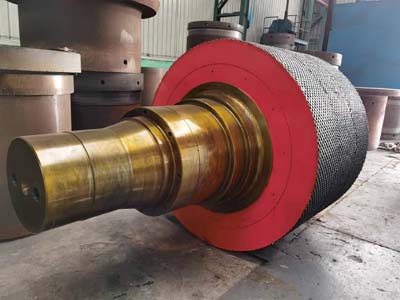
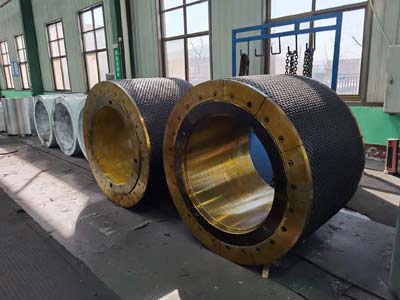
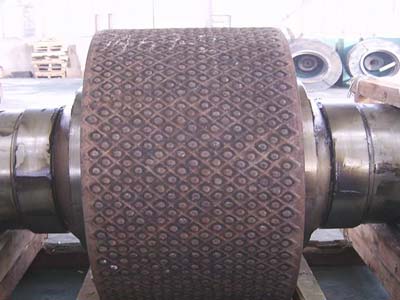
Manufacturing process
1) Design a new roller shaft according to the thickness of the roller shaft, and arrange forging
2) Roller shaft forging, heat treatment and processing
3) The roller shaft is processed to the inner diameter of the design size -10mm, and surfacing welding is carried out
4) After the surfacing welding, wait until the roller shaft is completely and slowly cooled to room temperature, and carry out secondary processing of the inner hole of the roller shaft
5) Roller shaft inner hole finishing
6) Roller shaft preheating
6.1) The roller shaft and the roller shaft are shrink-fitted, and the interference fit method is adopted.
6.2) Slowly cool down to room temperature after installation.
7) Paint coating
In addition to the roller shaft, the key components of the roller press, the welding treatment of the base layer, transition layer and wear-resistant layer on the surface of the roller shaft is also very critical. If you use simple welding experience to do non-specialized welding, it is difficult to meet the promised wear life of the roller surface, and a large number of facts have also proved this point. AGICO Cement's advanced surfacing equipment, reliable testing equipment, perfect production technology and process, and decades of welding experience ensure the wear-resistant quality and life of the roller shaft surface of the manufacturing roller press.