Industrial Filter Bag
Industrial filter bag from AGICO group's smart factory
As the world becomes more environmentally conscious, industries are being pressured to become more eco-friendly. In China, one company is leading the way in environmental protection enterprise. AGICO Group is the only enterprise in China that covers the entire industrial chain of production, from wire drawing to bag making, with a focus on sustainability.
Sophisticated Production Equipment for Quality Control
Each process in AGICO's production line is equipped with advanced and sophisticated production equipment to ensure high-quality control. This ensures that their products meet the highest industry standards. The intelligent factory is built with 121 lean production processes, combining automation, information technology, and lean management. The factory incorporates intelligent manufacturing into every production process and procedure, achieving fully automated technology transformation from wire drawing, spinning, weaving, and filter bag processing. This technology replaces human vision with machine vision, making production more efficient and accurate.
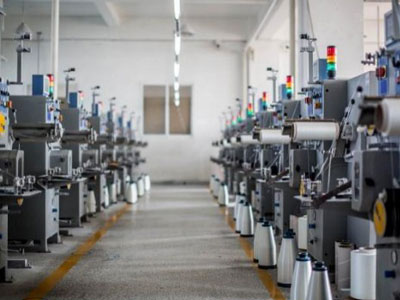
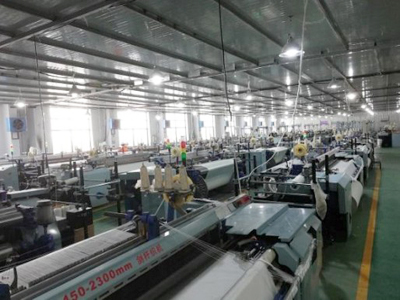
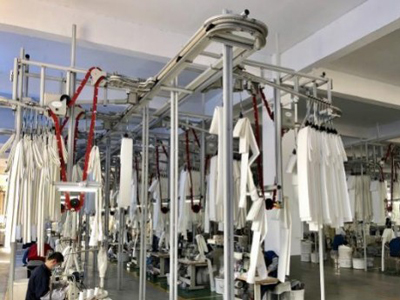
Powerful Scheduling and Management Systems
AGV scheduling system and MES system are used to connect the entire production system, from people to machines, materials, methods, and environment. This forms an intelligent, transparent, and lean production command center with AGICO characteristics. This system allows for more accurate tracking and scheduling of materials, which leads to a reduction in waste and a more sustainable manufacturing process.
Focus on Quality Control
The AGICO Group places a strong emphasis on quality control. They have passed ISO9001 series quality management system certification, 14001 series environmental management system certification, and 18001 series occupational health and safety management system certification. This shows their commitment to meeting high standards for quality control, environmental protection, and safety in the workplace.
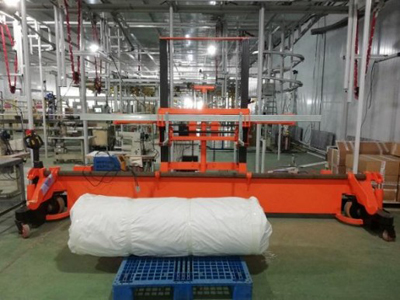
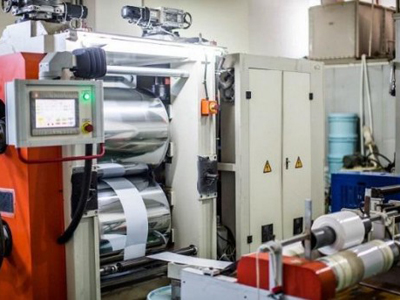
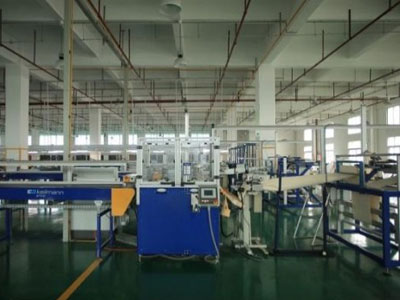
The AGICO Group is a company that is leading the way in environmental protection in China. Their focus on sustainability and quality control is evident in every aspect of their business. By incorporating advanced technology and efficient management systems, AGICO is able to maintain a sustainable manufacturing process while meeting the highest industry standards. As the world becomes more environmentally conscious, companies like AGICO will continue to pave the way for a more sustainable future.
Our industrial bags
Industrial Filter Bags for High Temperature | |||
![]() Acid resistant fiberglass filter bag with membrane | ![]() Alloy ferrosilicon reverse blow 10 meter fiberglass filter bag | ![]() Aramid needle felt filter bag | ![]() Corrosion resistant high temperature fiberglass filter bag |
![]() Fiberglass composite needle felt filter bag | ![]() High silicon (modified) filter bag with membrane | ![]() P84 polyimide glass fiber composite needle felt filter bag | ![]() P84 polyimide aramid composite needle felt filter bag |
![]() P84 polyimide needle felt filter bag | ![]() Texturized fiberglass filter bag with membrane | ||
Industrial Filter Bags for Medium Temperature | |||
![]() PPS (polyphenylene sulfide) antistatic needle felt filter bag | ![]() PPS (polyphenylene-sulfide) PTFE polytetrafluoroe thylene composite needle felt filter bag | ![]() PPS (polyphenylene-sulfide) superfine+PTFE (polytetrafluoroethylene) composite needle felt filter bag | ![]() PPS polyphenylene sulfide needle felt filter bag |
![]() PTFE (polytetrafluoroethylene) membrane coated needle felt filter bag | |||
Industrial Filter Bags for Low Temperature | |||
![]() Acrylonitrile homopolymer fiber (acrylic) filter bag with membrane | ![]() Polyester anti-static needle felt filter bag with membrane | ![]() Polyester needle felt filter bag | ![]() Polyester needle felt filter bag with membrane |
![]() Polyester waterproof, oil-proof, anti-static needle felt filter bag | |||
Bag Cage | |||
![]() 304 stainless steel bag cage | ![]() Galvanized bag cage | ![]() Organosilicon bag cage |
Filter Bag Processing Standards and Fine Stitching Techniques
At AGICO Group, our filter bag processing meets industry standards such as HJ/T326-2006 and GB/T 12625. We use CNC cutting machines to ensure stable and accurate dimensions during the cutting process. Our bag tube is sewn using a continuous production line to improve the overall quality of our product. Additionally, the bag mouth uses a stainless steel ring for added durability.
To ensure that our filter bags can be installed without gaps, we make sure that the upper and lower pieces of the bag body lines are flat, and the bag mouth and bag bottom joints are evenly folded. We use a three-needle stitching process for the bag body with high-quality, high-temperature-resistant, corrosion-resistant, and high-strength sewing thread. Even strong acids and alkalis have difficulty corroding or damaging it, ensuring that the bag will not tear due to spray blowing.
We take quality control seriously and follow strict guidelines in every step of our production process. Each process is managed according to the ISO9001:2015 quality management system standards. We have over 50 steps from raw material inspection and cleaning to finished product warehousing, with each step having key quality control points to strengthen our quality control during production. We have established a four-level inspection system of "employee self-inspection, workshop inspection, quality inspection, and random inspection" and adhere strictly to the principle of "no turning, no warehousing, and no factory shipment" for defective products. Our ultimate goal is "zero defects, zero complaints, and zero returns."
At AGICO Group, we are committed to providing the highest quality filter bags to our customers. Our fine processing techniques and strict quality control measures ensure that our products meet industry standards and exceed customer expectations.
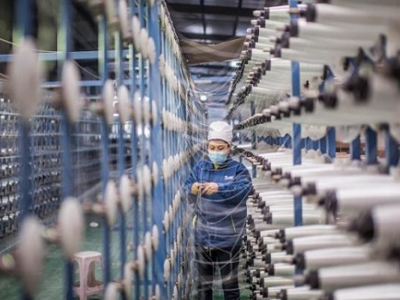
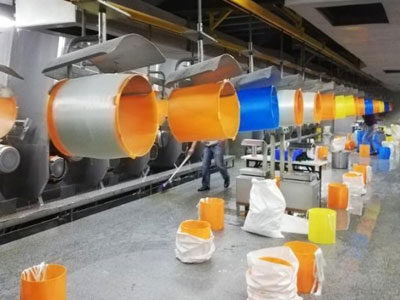
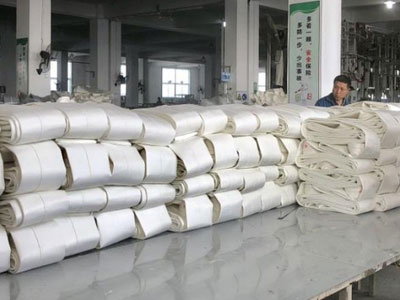
Manufacturing process of high-speed needle punching machine for filter bag production
The manufacturing process of a high-speed needle punching machine for filter bag production involves several steps. First, Polyphenylene sulfide (PPS) and ultra-fine fiber are opened, carded, and laid out as a web. Then, a PPS fiber base cloth undergoes pretreatment to become a high-performance PPS fiber base cloth. Another batch of PPS and ultra-fine fiber is opened, carded, and laid out as a web.
Next, pre-needle punching is done, followed by four primary needle punchings, PTFE impregnation, and PTFE film covering. The surface layer of the resulting PPS + ultra-fine fiber coated needle punched felt filter bag is made of PPS fibers, which are needle punched with high-performance PPS base cloth. PPS fiber has good spinability, improving the composite fastness and overall strength of the filter material.
The base cloth of the filter bag is made of high-strength PPS long fibers, woven into a high-strength PPS base cloth to ensure that the filter material has sufficient mechanical strength. After undergoing pretreatment and heat setting, the high-performance PPS base cloth with excellent physical and chemical properties and stable dimensions is produced.
Needle punching
The needle punching process involves mixing two high-quality fibers with the high-strength base cloth using our company's mature needle punching technology and Germany's DILO automatic equipment. This creates a needle punched filter material with good flexibility and excellent cohesion, significantly improving the composite fastness and overall strength of the filter material.
After the PPS + ultra-fine fiber coated needle punched felt filter material is produced, our company uses a unique post-processing formula called "Polytetrafluoroethylene (PTFE) mixed solution" for this working condition. The product is treated with water and oil repellency and PTFE impregnation, and then subjected to high-temperature sintering treatment. This fully wraps the surface of each short fiber in PTFE emulsion, playing a protective role of nano-coating. This significantly improves the overall anti-oxidation, corrosion resistance, temperature resistance, and size stability of the filter material. The water repellency of the filter material is enhanced, the filtration accuracy is improved, and the service life of the filter material is extended.
The three-dimensional structure of the filter material is not only conducive to the rapid formation of a dust layer but also does not have a direct passage of pores after dust collection and cleaning. This ensures stable dust collection efficiency, and the dust removal rate is higher than that of general woven filter materials. The dynamic dust collection rate can reach over 99.9% - 99.99%.
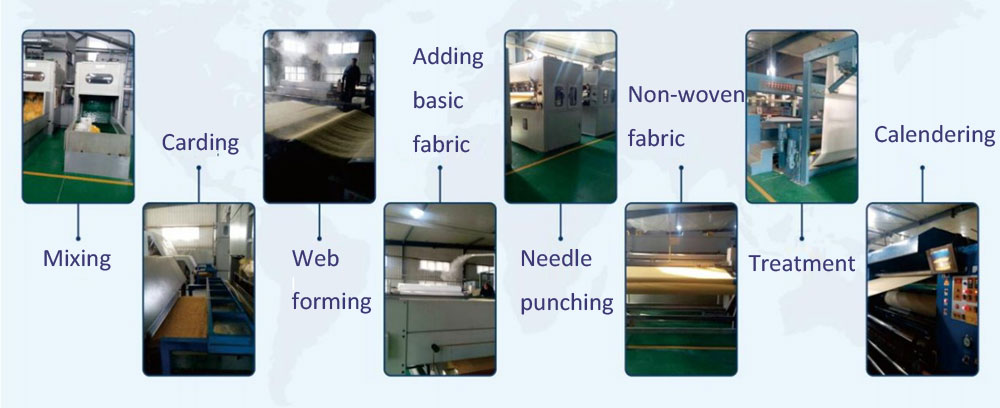