shell for grinding roller
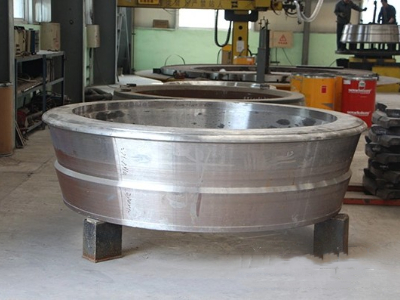
Shell for grinding roller
Weight: 3-20T
Material: ZG30Mn
ApplicationVertical roller mill
Customizable: Yes
Certification: CE, ISO 9001:2008
Standard: ASME, GOST
Surface Treatment: Polishing
Manufacturing Process: Casting
Material: Cast Steel
Because the vertical mill and its components work in the environment of high temperature, dust and moisture and chemical reactions for a long time, they will be impacted, vibrated, rubbed, and eroded under different loads during operation. Therefore, the materials used in production may naturally wear or crack and may eventually lead to equipment or components being scrapped. The shell for grinding roller is an important part of the vertical mill, and is mainly used for the grinding material of the vertical mill. The quality of the shell for grinding roller directly affects the production efficiency of the vertical mill and the economic benefit of the manufacturer.
Vertical mill is a grinding equipment widely used in electric power, mining and building materials industries. The shell for grinding roller is the grinding medium in the mill, so the it should have both high wear resistance and high toughness. There are many disadvantages of traditional materials, or the wear resistance is not enough, or the cost is too high.
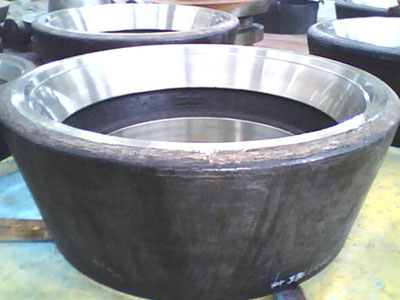
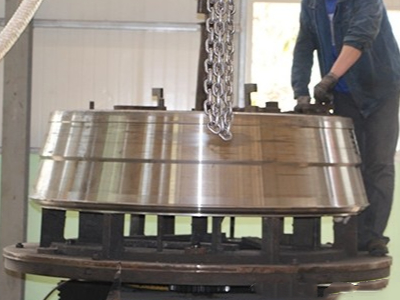
.jpg)
Advantages of our shell for grinding roller
1. AGICO Cement mainly uses high-chromium cast iron wear-resistant material to produce shell for grinding roller, which has good wear resistance and certain impact toughness. The production process of metal cold die casting is simple, low cost and low cost. Through the quenching + tempering dual-medium heat treatment process, advanced heat treatment process, and the company's systematic quality assurance system, the HRC hardness is guaranteed to be higher than 65.
2. AGICO Cement is a shell for grinding roller manufacturer integrating R&D, production and sales. The company is a standard-setting unit. The material is implemented in accordance with the ZMC-BTMCr20 of the GB/T33939-2017 standard. It is a well-known and trustworthy enterprise in China. There will be professional sales staff to answer questions during the sale, and support customization, and after-sale is guaranteed.
3. High wear resistance, strong comprehensive performance
It makes full use of the characteristics of surface hardening of high manganese steel or ultra-high manganese steel under high impact load, and the core still has good plastic toughness, preventing vertical grinding parts such as grinding rollers, roller sleeves and grinding discs from being subjected to strong impact loads and breakage.
4. Low wear and long service life
Carbide or ceramic particles evenly distributed in the working part have high wear resistance, effectively reduce the wear of the matrix high manganese steel, and increase the service life of vertical grinding rollers, shell for grinding roller, grinding table and other vertical grinding accessories by more than 1 times. The amount of replacement is significantly reduced.
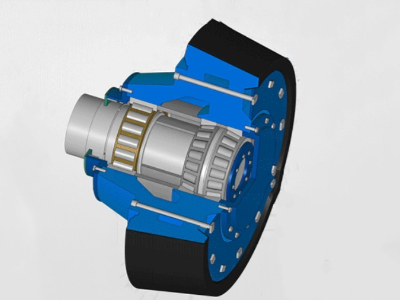
.jpg)
.jpg)
How to distinguish the quality of shell for grinding roller?
Shell for grinding roller is one of the most widely used wear-resistant materials, with high toughness and wear resistance. The vertical grinding roller sleeve is produced and cast by reasonably selecting the chemical composition of the Gr material and formulating the casting process and heat treatment process in combination with the solidification characteristics of high-chromium cast iron. So how to distinguish the quality of shell for grinding roller?
1. Look at the size. Due to the different models of the vertical mill, the required size of theshell for grinding roller of the vertical mill is also very different, so it is very important to ensure the overall size.
2. Look at the hardness. If the hardness is greater than 65, it can play a good wear-resistant effect during operation and improve the service life of the product. This is the most important point.
Third, look at the impact toughness value. Another important indicator is the toughness value. The toughness value reaches 7J (Joules). This standard is to prevent the shell for grinding roller from cracking during long-term operation.