ball mill head
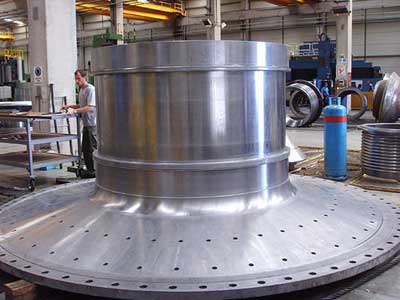
Process weight: 1-150ton
Heat treatment: Normalizing, Q&T
Surface Treatment: Painting, plating, polishing, transparent anti-rust oil
UT standard: EN, ASTM, DIN, etc.
Certificates: CE, ISO
Application: Cement ball mill, coal ball mill, slag ball mill, raw ball mill, gypsum ball mill, limestone ball mill
Standard: ANSI, ASTM, ASME, API, JIS, DIN, BS, EN, KS, UNI, SABS, GOST.
The ball mill head is one of the key parts of the ball mill. Its structure is relatively complex, the processing and manufacturing cycle is long, and the required processing and assembly precision is high. Therefore, the craftsmanship of ball mill head should be fully considered when compiling the process route.
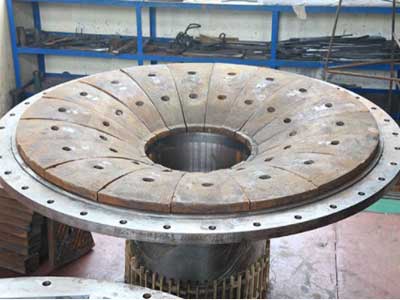
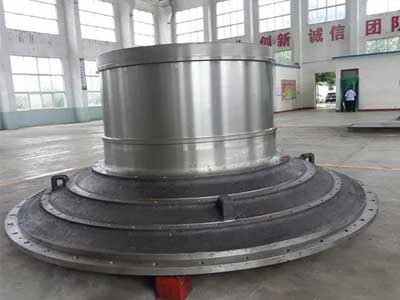
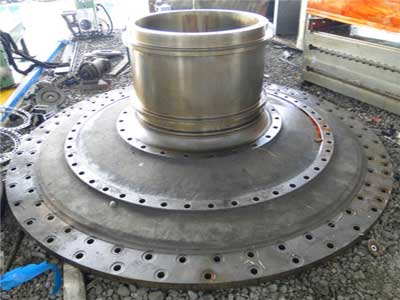
Common problem of ball mill head
1.The ball mill head are located at both ends of the barrel of the ball mill and are supported on the bearings. They are mainly used to support the material, barrel and medium. The fillet at the root of the end plate of the hollow shaft of the ball mill is the stress concentration part.
2.Since the inlet and discharge pipes and the hollow shaft are close to the cylindrical surface of the cylinder end, if the gap is too small, it is difficult to fold and fold, and if the gap is too large, it is easy for the slurry to enter the gap between the hollow shaft and the inlet and discharge pipes. The ore pulp entering the gap will wear the inner wall of the hollow shaft continuously with the rotation of the mill, and ball mill head with the hollow shaft will be scrapped prematurely.
3.After assembling, the ball mill end cap and the inlet (or discharge) material pipe are welded along the matching gap along the matching gap with the stainless steel electrode, which effectively solves the above problems. However, due to the redness of the welded seam, there is a stress concentration caused by welding, and the ball mill is affected by vibration, impact and alternating stress during operation. A new type of annealing furnace is used by AGICO Cement to improve stress and achieve good results.
Solution by AGICO Cement
1. Adopt high-quality raw materials and mature technology to solve the problem of excessive wear and tear.
AGICO has been engaged in the manufacture of ball mills for more than 20 years, and encountered many common problems in the industry during the production process. We continue to adopt new technologies and processes. The wear of the feed end cap is relatively common, but the products of AGICO have a much longer service life than the ball mill end caps of other companies which allowing customers to be assured of production.
2. Closely fit the parts, no leakage problem
Ball mill end cover produced by AGICO Cement can be adjusted to a certain extent for specific equipment, so that the end cover and the incoming parts are more closely fitted without gaps, which effectively prevents the material leakage problem caused by the insufficient fit between the end caps of some ball mills and the components.
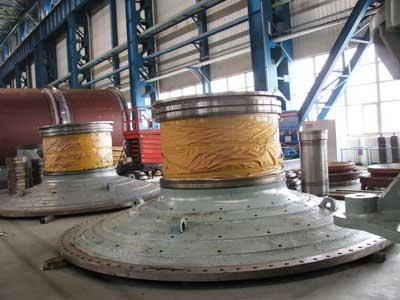
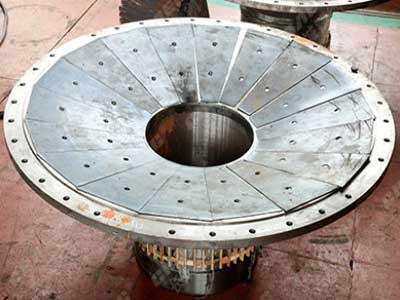