Common Material and Shape of Ball Mill Liner
Material of Ball Mill Liner
Currently, commonly used materials for ball mill liners are metal lining plates and wear-resistant rubber lining plates. The selection of suitable ball mill liner material depends on the different motion states of the materials being processed in the ball mill.
High Manganese Steel Lining Plate
Considered a first-generation wear-resistant material, with manganese content ranging from approximately 12% to 14%. It exhibits strong impact resistance, and its impact force can undergo hardening, increasing the original surface hardness from HRC20~HRC25 to above HRC40, with an impact value of up to 700Nm/cm2.
Despite its strong impact resistance, its hardening degree is not sufficient for withstanding high-intensity impacts. Additionally, high manganese steel lining plates have low yield strength, prone to plastic deformation, resulting in plate protrusion, and in severe cases, difficulty in disassembly.
The total lifespan of high manganese steel lining plates is approximately 5000-6000 hours, mainly used in medium-sized mills and rarely in large ball mills.
High Chromium Cast Iron Lining Plate
With wear resistance more than twice that of high manganese steel, it is a high-performance, long-life, and expensive wear-resistant material. High chromium cast iron is categorized into medium chromium cast iron and low chromium cast iron based on the chromium element. It is known for superior wear resistance, good high-temperature and corrosion resistance, but lower toughness and crack resistance compared to high manganese steel and medium to high carbon alloys.
High chromium cast iron lining plates are commonly used in large ball mills and serve as coarse material bin lining plates in medium and small ball mills.
Low chromium cast iron has inferior toughness and wear resistance compared to high chromium cast iron and is generally suitable for fine material bin lining plates in small mills.
Wear-Resistant Rubber Ball Mill Liner
Wear-resistant rubber lining plates are a new generation of wear-resistant materials with wear resistance reaching 128%, rebound reaching 80%, tensile strength reaching 23.5MP, and tear strength reaching 168N/mm. These characteristics are attributed to the rubber material, providing excellent resilience, fatigue resistance, chemical corrosion resistance, and shock absorption.
According to incomplete statistics, the wear resistance of wear-resistant rubber lining plates is approximately 1.5~4 times higher than that of high manganese steel lining plates. As a result, their service life is longer, and the replacement cycle is extended, thereby improving the operational efficiency of the ball mill, reducing maintenance frequency, and costs.
Additionally, the individual mass of wear-resistant rubber lining plates is light, generally around 20kg, significantly reducing the labor intensity in disassembly and installation compared to metal materials such as high manganese steel and cast iron. This also reduces the overall energy consumption of the ball mill by approximately 5%-10%.
However, wear-resistant rubber lining plates have poor impact resistance, are unsuitable for dry grinding environments, not heat-resistant, and not suitable for use in the coarse material bin of ball mills. They are suitable for use in grinding bins, fine grinding bins, wet ore grinding, and other environments.
In addition to the three commonly used lining plate materials mentioned above, there are also magnetic lining plates, alloy steel lining plates, cast stone lining plates, etc.
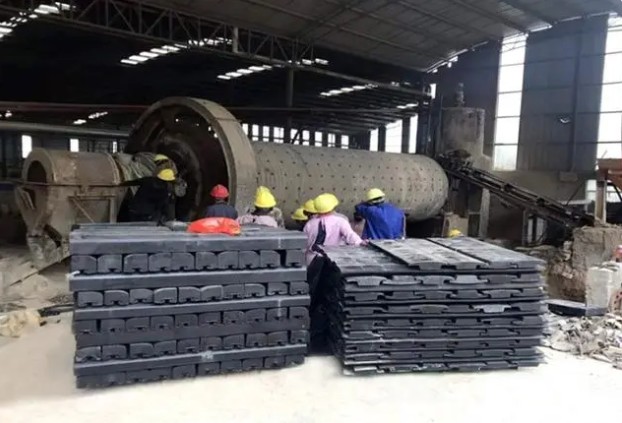
Shape of Ball Mill Liner
The shape of ball mill liners can be divided into nine major types: wedge-shaped, waveform, flat convex, flat, step-shaped, strip, rudder-shaped, K-shaped rubber lining plate, and B-shaped rubber lining plate. Among them, the following are commonly used:
Waveform Ball Mill Liner
Waveform ball mill liners are cast with a section resembling a wave node on a flat lining plate. For a wave node, the rising part is effective in lifting grinding media, while the descending part has some adverse effects.
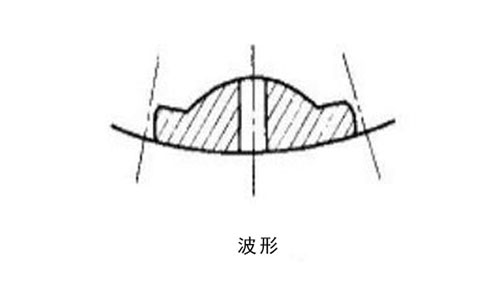
Flat Convex Ball Mill Liner
Flat convex ball mill liners are cast with a semi-circular or trapezoidal convex edge on the lining plate. It has the same effect as the pressure strip. Flat convex liners have greater rigidity and can be made of materials with greater ductility. When making liners with materials that have high ductility, the liner will bend without breaking bolts, avoiding this type of defect.
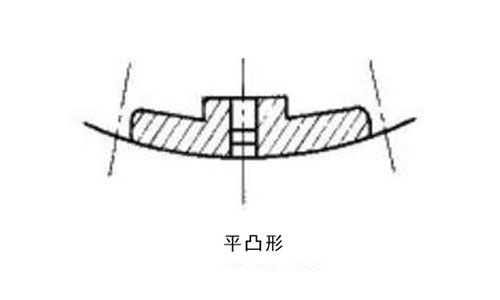
Flat Ball Mill Liner
Flat ball mill liners have equal thickness and some may have a scratched surface or patterns cast on them. The action of this type of liner on materials mainly relies on the static friction between the liner and the material. During the grinding process, material sliding may occur, reducing grinding quality, but it can increase the grinding effect. Therefore, flat ball mill liners are mostly used in fine grinding bins.
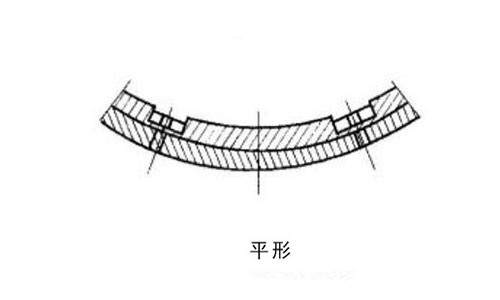
Step-shaped Ball Mill Liner
Step-shaped ball mill liners have a special shape that not only provides friction between the steel ball and the lining plate but also increases the adhesion between the ball and the liner.
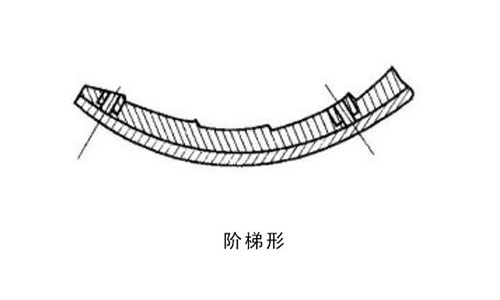
Strip Ball Mill Liner
Strip ball mill liners completely avoid the formation of circumferential wear grooves on the lining plate, significantly reducing the metal consumption of grinding media and lining plates.
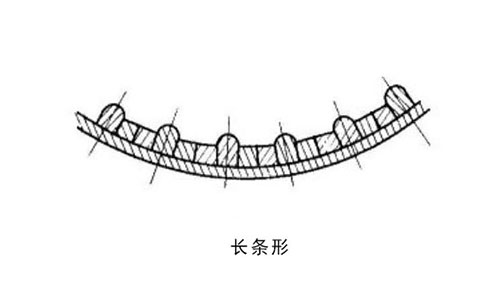
Rubber Ball Mill Liner
The use of rubber ball mill liners is based on the premise that the cylinder must have sufficient rigidity, and the inner surface must be smooth and round. The lining plate length and width tolerances should be controlled within 1mm. The lining plate must have sufficient strength, a smooth appearance, uniform quality, and sufficient wear resistance.
Rubber has a longer lifespan than steel lining plates, reduces electricity consumption by 5%-10%, avoids circumferential gaps in the lining plate, prevents slurry from washing the cylinder, thereby protecting the cylinder. Rubber lining plate bolts are not easily broken, the lining plate is tightly installed without slurry leakage, and rubber lining plates are lightweight, easy to maintain, operationally safe, reduce mill noise, and improve working conditions.
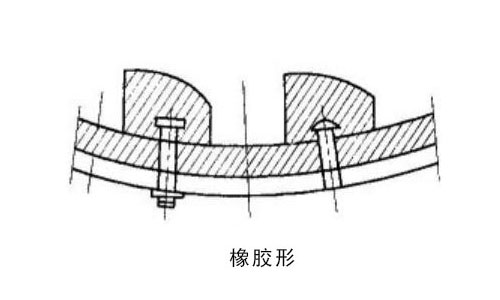