How to Ensure the Balance of the Rotor in a Hammer Crusher
A crusher rotor is a component of a crushing machine that is responsible for the breaking or crushing of larger materials into smaller pieces. The rotor consists of a central shaft that is equipped with multiple crushing tools such as hammers or blades that rotate at high speeds, creating an impact force that breaks the material.
The design and configuration of a crusher rotor can vary depending on the type of crusher and the intended application. For example, some rotors may have a single row of hammers or blades, while others may have multiple rows or staggered configurations.
The material used to construct the rotor is also an important consideration, as it must be strong and durable enough to withstand the high impact forces generated during the crushing process. Common materials used for crusher rotor construction include high-strength steel alloys and composite materials.
Proper maintenance and inspection of the crusher rotor is crucial for ensuring optimal performance and preventing damage or failure. Regular checks for wear and tear on the crushing tools, as well as proper alignment and balance of the rotor, are important measures to keep the crushing machine running smoothly and efficiently.
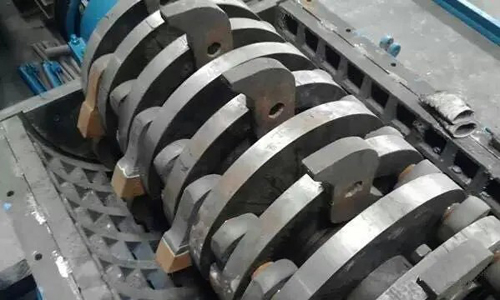
How to Ensure the Balance of the Rotor in a Hammer Crusher?
In the operation of a hammer crusher, it is important to maintain good balance of the rotor. If the rotor is not balanced properly, it will increase the wear of the hammer heads and require frequent replacement, which not only wastes time but also increases production costs. Therefore, it is crucial to ensure the balance of the rotor.
There are three main reasons for rotor imbalance:
- If the main inertia axis of the rotor does not coincide with the axis of rotation but is parallel to it, i.e., if the center of gravity of the rotor is not on its axis of rotation, then static imbalance will inevitably occur.
- If the main inertia axis of the rotor intersects with the axis of rotation, intersecting at the center of gravity of the rotor, i.e., if the axis of rotation and the geometric centerline of the rotor intersect, then dynamic imbalance will inevitably occur during rotation of the rotor.
These two types of imbalance phenomena will cause the rotor to produce a large dynamic load (i.e., bending moment) during rotation, causing unstable operation of the machine and deterioration of components such as the spindle, bearings, and frame. In particular, it will cause periodic impact loads on the bearings, leading to overheating and even damage. In addition, it will cause vibration of the machine. Rotor imbalance is mainly caused by poor manufacturing quality and assembly precision of rotor components. - At the same time, uneven wear of the hammer heads during operation is also a factor that affects rotor imbalance.
When designing a hammer crusher, attention should be paid to ensuring that the dynamic load of the crusher does not exceed the allowable value. After the rotor is assembled, a balance test must be performed. For rotors with a small length and a speed below 800r/min, only static balance needs to be done; for rotors with a larger length, dynamic balance must be done in addition to static balance. For users, when replacing the hammers, balance must also be done. The method is to weigh each hammer one by one, record the weight on the hammer, and also record it in detail on the record sheet.
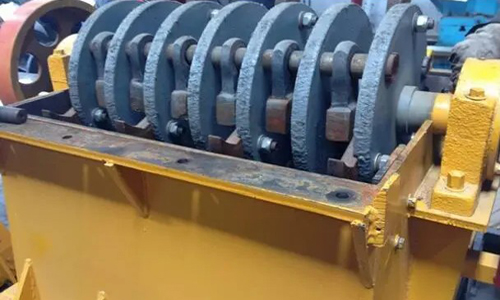
It is necessary to balance the corresponding two rows, i.e., the two symmetrical hammer heads, and the two hammer heads corresponding to the axial section should also be balanced. This is the simplest method.
If all the corresponding two rows of each hammer head are balanced, and there are only two unbalanced ones, and these two hammer heads are at both ends of the rotor, then a moment will be produced during rotation, causing dynamic imbalance and vibration. If the unbalanced masses are equal and opposite and are separated by 180 degrees, the axis of the rotor can reach a balance, and then rotate, but each unbalanced hammer head will produce a rotating centrifugal force, causing the rotor shaft to sway within the bearing. Therefore, it is necessary to minimize the distance between the hammer head and the rotating parts.