Operating Precaution and Issue in Industrial Dust Collector Bags
Operating Precautions for Dust Collectors
❏ Fuel Control
Changes in fuel composition can lead to variations in the exhaust gas composition. For example, an increase in sulfur content in coal fuel can alter the exhaust gas properties, causing corrosion and damage to industrial dust collector bags. Similarly, changing the fuel from diesel to petroleum coke can also alter the exhaust gas composition, affecting the lifespan of industrial dust collector bags.
❏ Control of Exhaust Gas Temperature
Strict control of the inlet temperature of the dust collector is essential to ensure the safe operation of industrial dust collector bags. The temperature resistance of industrial dust collector bags is determined by their fiber material. Each type of fiber material has an upper temperature limit. When the exhaust gas temperature exceeds the bag's upper limit, the bags may shrink or even burn.
❏ Control of Raw Material Handling
Industrial furnaces often process varying raw materials, leading to changes in exhaust gas composition. For example, the exhaust gas generated by industrial drying kilns depends on the material being dried. When corrosive substances form in the exhaust gas, it directly impacts the lifespan of industrial dust collector bags.
❏ Control of Ammonia Injection Amount for DeNOx
During the DeNOx process in industrial furnaces, excessive ammonia injection can lead to ammonia leakage. Ammonia escaping into the exhaust gas can react with SO3 to form ammonium bisulfate, a highly viscous ammonium salt. When it encounters industrial dust collector bags, it can clog the bags, leading to increased resistance and, in severe cases, preventing the dust collector from functioning properly.
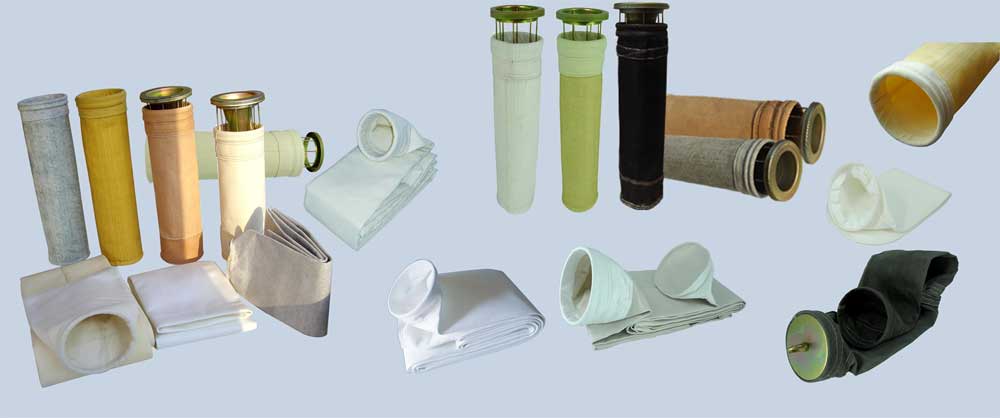
Common Issue of Industrial Dust Collector Bags
I. Industrial Dust Collector Bags Blockage
Cause Analysis:
(1) Leaks in the baghouse or condensation due to low exhaust gas temperatures, or water leakage in the ducts, resulting in wet industrial dust collector bags and dust sticking.
(2) Excessive filtration speed, very fine or coarse dust with adhesive properties, leading to poor cleaning efficiency of industrial dust collector bags.
(3) Short cleaning time and cycle of the dust collector's pulse jet cleaning.
(4) Insufficient pressure in the dust collector's pulse jet cleaning, making it difficult to remove the dust.
Remedies:
(1) Install insulation or heating functions for the dust collector and provide rain and wind protection.
(2) Set a reasonable filtration speed based on filter material properties.
(3) Monitor the pressure drop in the dust collector and adjust the pulse jet pressure and cleaning cycles.
II. Industrial Dust Collector Bags Burnout
Cause Analysis:
(1) High-temperature particles or electrostatically charged dust entering the dust collector can cause sparks that burn small holes in the industrial dust collector bags.
(2) Spontaneous combustion of accumulated dust in dead zones and hoppers of the dust collector, leading to local or full-box burnout of industrial dust collector bags.
Remedies:
(1) Install flame suppression devices to prevent direct flames from entering the dust collector.
(2) Reduce dead zones inside the dust collector and regularly remove accumulated dust, leaving some sealed to prevent air leakage.
III. Industrial Dust Collector Bags Corrosion
Cause Analysis:
Corrosion is caused by damage from acidic or alkaline substances, resulting in local or overall brittleness and reduced strength or hole formation in industrial dust collector bags.
Remedies:
Choose filter material materials suitable for the working conditions and control changes in exhaust gas composition.
IV. Mechanical Damage to Industrial Dust Collector Bags
Cause Analysis:
(1) Friction and punctures on the frame surface due to roughness and sharp welding marks.
(2) Improper storage, transportation, and installation.
(3) Excessive pressure in the pulse jet cleaning, causing bag wear.
Remedies:
(1) Pay attention to frame maintenance and keep its surface smooth.
(2) Properly package, handle with care during transportation, and avoid bending. Handle with care during installation to prevent damage, and avoid dragging on the ground.
(3) Adjust the pulse jet pressure.
V. Weak Pulse Valve Jetting
Cause Analysis:
(1) Large throttle holes in the diaphragm or the presence of pinholes in the diaphragm, and partial blockage of the exhaust holes.
(2) Low air pressure from the air source.
(3) Misalignment or blockage of the cleaning nozzles.
Remedies:
(1) Replace the diaphragm and clear the exhaust holes.
(2) Increase the air pressure from the air source.