Reasons and solutions for vibration of kiln girth gear
1. Cause Analysis
(1) The rotary kiln itself is a heavy-duty continuous operation equipment. In addition, the pinion and the kiln girth gear generally work in a dusty environment, and the working surface is easily worn. After the kiln girth gear’s surface is worn, its tooth shape will be destroyed, which will increase the tooth side clearance, which will easily cause shock and vibration; after the tooth surface is worn, a new top clearance will be formed, and the center distance between the kiln girth gear and the pinion will change slightly. Vibration occurs due to the phenomenon of top tooth tipping. From the scene, the pinion gear is seriously worn, and the height of the ground on the tooth surface is about 5mm. The irregular wear on the surface of the kiln girth gear is also quite serious, and the gear meshing is far from the standard requirements.
(2) Due to years of high temperature oxidation and corrosion on the part where the kiln girth gear is installed on the cylinder, the thickness of the spring plate is reduced from the original design 30mm to 18~200mm. Three of the spring plates are seriously deformed, and the other two adjacent ones have longitudinal cracks. The shaft hole is seriously worn, and the larger one is 60mm larger than the original; due to the deformation of the spring plate and the increasing size of the pin shaft hole, the kiln girth gear changes from local loosening to local sinking, and then slowly develops into overall sinking, and the large and small gears The phenomenon of top teeth is becoming more and more serious. The radial runout of the kiln girth gear reaches 90mm, and the end face runout reaches 70mm, which causes the gear vibration to increase sharply.
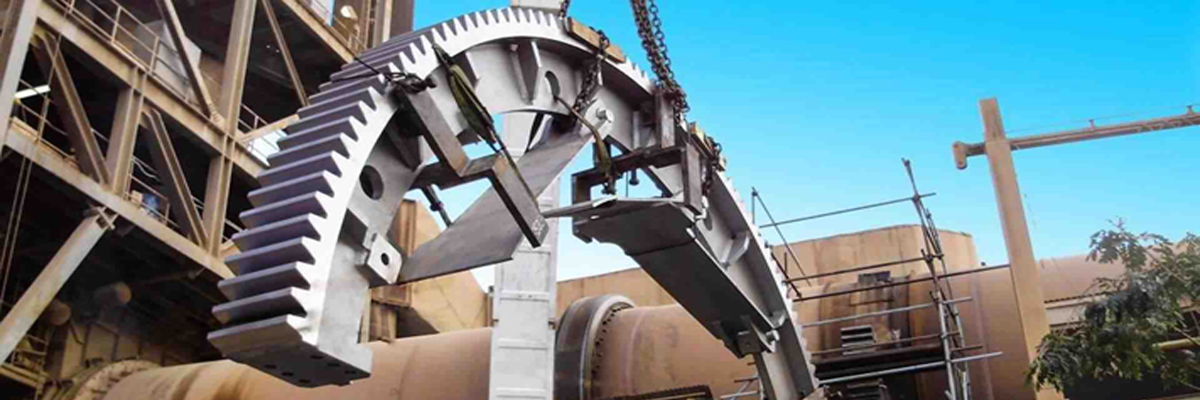
2. Solutions
(1) Grinding the gears, rough grinding the tooth surfaces of the large and small gears with an angle grinder to eliminate the steps, then slowly rotate the kiln, and then use a straight grinder to grind the high points of the large and small gear teeth.
(2) Use gas cutting to cut the deformed spring plate, the cracked spring plate and the cylinder body, and use the jack to reset the sinking gear ring.
(3) Correct the deformed spring plate with flame, repair the cracked spring plate by repair welding, and reinforce all thinned spring plates with reinforcing ribs.
(4) Adjust the fit of the kiln girth gear spring plate and the pin shaft. Since part of the pin shaft and pin shaft hole have been worn out, use a reamer to repair the pin shaft hole that has become an elliptical hole, and re-measure the size of the repaired pin shaft hole. The pin shaft is processed, the spring plate hole and the pin shaft are matched with H7/k6 transition fit, which increases the stability and firmness of the pin shaft and the pin shaft.
(5) Replace the corresponding screws to improve the stability of the kiln girth gear.
(6) After adjusting the axial and radial runout of the kiln girth gear, re-weld the cut spring plate and the cylinder.
(7) Apply red dan powder for grinding in a rotary kiln, so that the contact of the tooth surface in the height direction is greater than 50% and the contact in the length direction is greater than 60%, and the tooth tip clearance is checked by the lead pressing method. The tooth tip clearance is controlled according to the above-mentioned empirical formula. The result is exactly what is required. The axial and radial runout of the kiln girth gear are reduced to about 3mm, which basically meets the installation requirements.