Safe Operation and Maintenance Procedures of Hammer Crusher Machine
Equipment Name: Ring Hammer Crusher Machine
Ⅰ Safe operation
1. The crusher can only be fed when it is running normally, and it is not allowed to start the machine after feeding.
2. The feeding work should be stopped before stopping the machine, and the motor can only be turned off after the materials in the crushing chamber are completely crushed and cleared.
3. Regularly check the condition of the sieve plate, if there is any blockage, it should be removed immediately.
4. When the machine is running, it is strictly forbidden to carry out any adjustment, cleaning and maintenance work.
5. It is strictly forbidden to put unbreakable materials into the machine, so as not to damage the machine.
6. When the machine is overhauled, the power supply should be cut off first.
7. During operation, do not touch the high rotating pulley, a protective cover should be added to the pulley (by the user), and the motor must also have rainproof and sunscreen devices.
8. During operation, never open the side cover to avoid materials flying out and hurting people.
9. When there is an abnormal situation, stop the machine immediately for inspection.
Ⅱ Maintenance
1. When assembling or replacing the hammer head, the rotor must be kept balanced. The total weight of the 8 hammers on each hammer shaft should be equal to the total weight of the hammers on the corresponding hammer shaft, and the deviation of the total weight should not exceed 0.1kg.
2. The liner is a vulnerable part that protects the crushing frame and prolongs its life. When the liner is worn to affect normal use, it should be replaced in time. 3. Check the machine once a year, replace the damaged parts, and replace the grease.
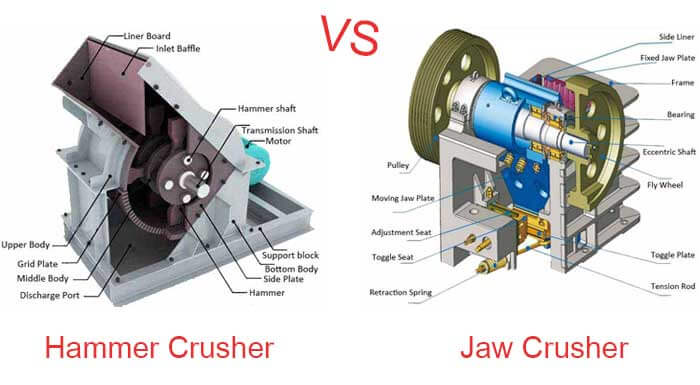
Safe operation and maintenance procedures of hammer crusher machine
Equipment Name: Drying Hammer Crusher Machine
1. Before the hammer breaker is in operation, hot air and materials must not be sent to the hammer breaker.
1.1 After the feeding is stopped, the hammer breaker should continue to run for 1.5 hours before the official shutdown. When the hammer is running, the cooling system must not be turned off.
1.2 In the event of a sudden power failure, when the internal temperature of the hammer breaker is higher than 200°C min, the rotor body should be manually rotated 180°.
2. Driving and parking sequence:
2.1 The starting sequence of this machine must follow the sequence of the reverse production process, namely: temperature monitoring device and water spraying device → drying crusher → high temperature fan → rotary kiln → filter cake feeder → belt conveyor → vacuum suction filter .
2.2 Shut down to implement the sequence of production process, namely: vacuum suction filter → belt conveyor → filter cake feeder → rotary kiln → high temperature fan → drying crusher → temperature monitoring device and water spraying device.
3. Interlock requirements
3.1 The temperature conditions of all bearings of this equipment, including the rotor main shaft bearing and the main motor bearing, are interlocked with the system stop and start. The rotor spindle bearing is equipped with a platinum thermal resistance, and the electrical control system must have a temperature display and control function suitable for it.
3.2 When the temperature rise reaches 70°C, it will alarm, and when it reaches 90°C, it should stop.
3.3 When the outlet air temperature exceeds 220°C, the water spray device starts.
3.4 Alarm when the main bearing cooling water flow rate is less than 2x20L/min.
3.5 When the spindle proximity switch detects an abnormal signal, it will alarm.
3.6 The crusher should be interlocked with the feeding equipment. When the crusher stops, the feeding equipment and related equipment should stop at the same time.
3.7 The cooling machine must be started simultaneously with the rotor. After the rotor stops (5-10) min, then turn off the fan.
3.8 The cooling machine must start to circulate when the rotor starts, and stop after (5-10) min after the rotor stops.
3.9 A speed monitor is installed at the coupling. When the speed monitor detects abnormal signals, it should call the police or (in serious cases) stop the machine.
4. Other requirements
It is strictly forbidden to feed metal foreign objects such as steel brazes and iron blocks into the crusher. If you find any metal foreign objects mixed in or hear the abnormal sound of metal foreign objects impacting the machine, you should stop immediately. After the crusher is completely stopped and fully cooled, open the machine. Remove foreign matter, and make necessary speed adjustments to the working parts in the machine cavity.
Operating Instructions
1. Normal operation and inspection
During the normal operation of the crusher, the maintenance personnel regularly check it, so that faults can be found in time, problems can be determined and hidden dangers can be eliminated, and sudden shutdown accidents can also be avoided.
2. Fault generation and processing
At the airport work site, it is recommended to set up an emergency stop switch to avoid equipment damage. In addition, safe operation rules and safety precautionary systems are set up on site.
3. Long-term downtime
Due to various factors, during the operation of the crusher, there is a long downtime. For this situation, it is not enough to turn off the power alone, and preventive measures are needed to ensure that there is no trouble in restarting after shutdown.
3.1 Early preventive measures for long-term shutdown;
A. Rotate the crusher to empty the internal materials;
B. Clean the old grease on the bearings and seals, and add fresh grease;
C. Fix the rotor;
D. If necessary, cover the dangerous part of the equipment to prevent rust and damage;
E. In particular, provide long-term protection for the motor and reducer according to the supplier's suggestion.
3.2 Preparatory measures for restarting.
A. Remove all protective coverings;
B. Remove the grease from all bearings and seals, and refuel according to the requirements of this manual;
C. Remove the rotor fixing parts;
D. Check the transmission system and reinstall the expansion sleeve if necessary.